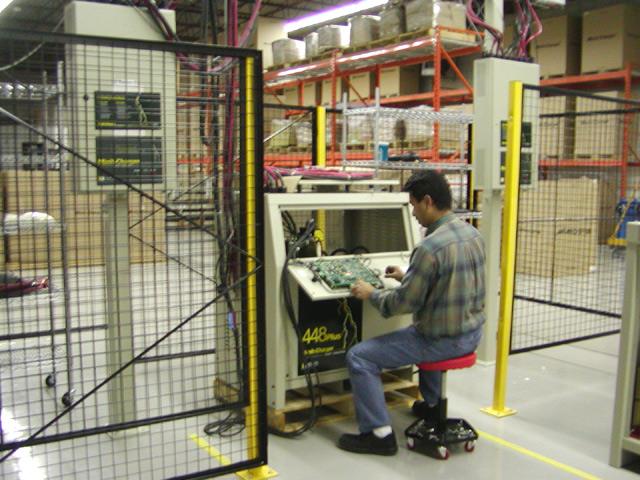 Minit-Charger undergoing pre-shipment testing at the Minit-Charger manufacturing centre. |
In the 1990s, California, USA, established a series of mandates to reduce air pollution from transport sources. That prompted US companies to invest millions of dollars in developing battery-powered cars and buses. Edison Minit-Charger and Posicharge are among the players that developed a new type of battery charging. The technology, fast charging, is now used in forklifts, not cars.
Christine Liew reports.
From cars to forkliftsPeter Michalski is managing director of California-based Minit-Charger, the company that was first to trial fast chargers on forklifts at a Ford assembly plant in Michigan in 1996.
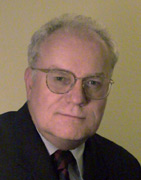 Peter Michalski, managing director of Minit-Charger. |
Michalski said the forklift industry was now the main market for fast chargers. His company's customers include automotive plants, frozen food processors, flooring manufacturers, pharmaceutical manufacturers, food retailers, beverage bottlers and other distribution centres. US home improvement retailer Home Depot has been a Minit-Charger customer since 1999.
"The high-powered fast charger was originally created for use in electric cars to recharge the battery in just a few minutes, no longer than it would take to refill a car's gas tank," he said.
However, development of fast chargers for electric cars raced ahead of development of the cars themselves. "Most of the cars didn't go more than 50 miles (80.5km) to 100 miles (160.9km) before they had to be recharged. Batteries for fast chargers had to be sufficiently large to be used in electric cars and fast chargers were too expensive for cars. Eventually, the limited range the cars offered did not win sufficient mainstream customer attention in the USA.
"Subsequently, some customers in the forklift industry saw the opportunity to apply fast-charge technology to their forklift fleets to reduce operating costs."
Michalski said fast charging was still in its infancy but rapidly gaining acceptance in the materials handling industry. His company's first commercial fast-charge applications for forklifts in 1998 were for sit-down riders, reach trucks and pallet jacks for Nestle. Based on customer operating profiles, Michalski said the potential US fast-charger market was more than USD150 million a year or 15,000 to 20,000 forklifts converting to fast charge annually.
What is fast charging?Fast charging charges a battery on average four times faster than conventional or "slow chargers". It recharges batteries at high charge rates at opportune times during a work shift. When an operator takes a break, has lunch or changes shifts, the forklift is idle and the battery is charged. The operator is encouraged to connect and charge frequently. The high charge rates provided by the fast charger during charging periods replace energy used during work operations, creating a balance that allows the forklift to run on a single battery all day.
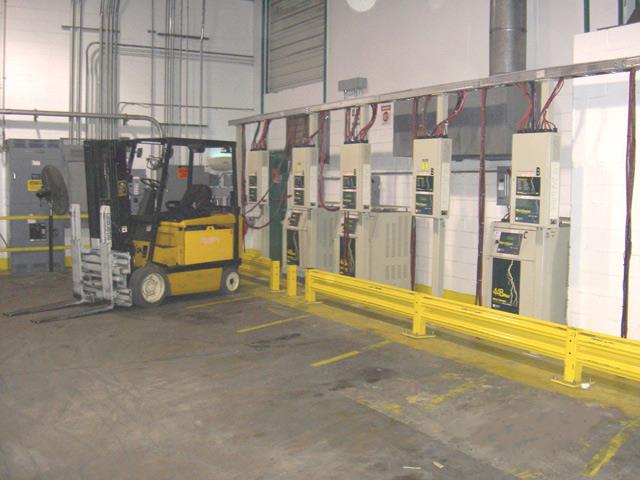 The multi-station Minit Charger system. |
Fast chargers are connected directly to battery connectors mounted on the forklift. Recharging occurs quickly because a higher charging current (from 400 amps to 600 amps) is delivered by the fast charger, about three to five times higher than the typical current delivered by conventional charging systems.
Michalski said while the industry had not yet agreed on a clear definition of a fast charger, there was a growing consensus that chargers with output rates of 300 or more amps at normal operating temperatures had the charge control sophistication and charger power level to be distinguished as fast chargers.
"Proper use of a fast charger results in a forklift operating at a 30 per cent to 80 per cent state of charge. It's called the sweet spot. The forklift battery, when charged by an operator between shifts, never has a 100 per cent state of charge but the forklift will still operate normally. The forklift will be charged to 100 per cent at the end of the day and equalised on weekends to ensure good battery life," Michalski said.
An electric forklift cuts off its operation at a 20 per cent state of charge, so the state of charge must be maintained above 20 per cent. Michalski said a forklift would operate normally even though its state of charge was less than 100 per cent. In that way it is like a car. The petrol tank doesn't have to be full for it to operate.
Forklift fleets that require batteries be changed during work shifts and that work multiple shifts could benefit from investing in the technology. Michalski claims savings of more than 50 per cent could be realised, compared to conventional charging. The equipment, a charging station and a fast-charge-ready battery, would be paid for in less than two years.
Michalski said users needed to consider the impact of installing high-power fast chargers.
"Not all facilities have an abundance of extra power for fast chargers. Fast-charger manufacturers have developed single and multi-station chargers to minimise the impact of the extra power load and running circuits to chargers.
"Most battery manufacturers now offer fast-charge-ready batteries. The main difference between a standard battery and a fast-charge battery is the addition of upgraded cables and double inter-cell connectors that allow use of higher charge rates.
"To facilitate watering, single-point watering systems are installed to avoid lifting the forklift battery cover. Watering is typically done once a week at the weekend. These additions generally add 10 per cent to 20 per cent to a standard battery's cost," Michalski said.
What are the benefits?Michalski said the benefits of fast charging stemmed not just from changing the charger type but the entire battery charging work process.
"With a fast charger, a warehouse can eliminate cost components found in the traditional battery changing work process. For example, there is no need for a battery changing room, a battery change machine, a battery room attendant or extra batteries for each forklift. Most importantly, time used to drive to and from the change area and perform the battery change becomes available for productive work that adds to the bottomline," he said.
Michalski claims fast chargers provide safety benefits. Eliminating frequent handling reduced the risk of accidents and injury.
"Reducing aisle traffic accidents with other forklifts or pedestrians as forklifts race to change batteries during a work shift is a significant improvement to workplace safety."
Despite the pluses of fast charging, Damien Declercq, Exide Technologies' marketing director for south and west Europe, says it's not all positive.
"There is clearly a demand for fast charging. [But] charging in a shorter period to increase battery running time will have an effect on its life cycle. You have to find the right balance between fast charging and the battery's life cycle."
He said Exide, which manufactures fast chargers, had a policy of not promoting fast charging to the entire market.
"Very few inquiries are received for very fast charge. This is a niche market and, as every customer has unique applications, no standard solutions can be offered.
"The higher the charging time the better for your battery.
"You can't just shorten the charging time by increasing the charging current without an effect on the battery. The main point is the battery's temperature. Charging a battery in a shorter time means transferring more energy than with a standard profile. If the charging process is not correctly monitored, battery temperature increases. Higher working temperatures mean shorter life cycles. Any request for fast charging needs a deep investigation from qualified application engineers," Declercq said.
Michalski said Minit-Charger's eight years' fast charging experience had shown battery life for fast-charge batteries was equal to or better than standard batteries.
"All other things being equal, battery life has more to do with the number of amp-hours put through the battery than any other criteria. For example, in the same fleet operation, customers have seen conventional battery life of six calendar years with the battery used for one shift a day.
"After converting to fast charge, the same operation went for more than three years but with the battery used in two shifts daily. With fast charging, counting charge cycles has gone by the wayside. With Minit-Charger, onboard battery modules track each instance of charging and discharge in real time and an accurate battery health status is available to the customer at any time. The information is like an odometer on your car, and uncertainty of battery usage and life is eliminated," Michalski said.
Minit-Charger used patented charge control technology based on the multi-parameter sensing of battery cells, which avoided battery overheating. The technology monitors battery cell status and determines the precise charge acceptance capability of the battery. An on-board battery module then communicates control instructions to the charger.
Gid Herman, product manager from PosiCharge, which launched a fast charger in 1999 under the name of its parent company Aero Vironment, said tests had shown fast chargers did not harm batteries.
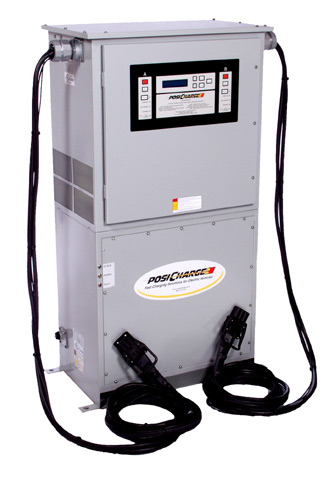 The Posicharge dual vehicle charger. |
"A few years ago, when the technology was just getting started, there were concerns fast charging might be harmful to batteries but numerous audited tests and close collaboration with battery manufacturers has demonstrated that is not the case. Just about every battery manufacturer offers a comparable warranty on its batteries, whether they are fast charged or conventionally charged," Herman said.
The PosiCharge fast charger employs a temperature foldback mechanism that constantly reads the temperature and dynamically regresses the charge rate to ensure safe temperatures while continuing to charge the battery.
"There is evidence intelligent charge systems that closely monitor the battery actually extend its life," Herman said.
Ford Motor Company has committed to replace its battery rooms with PosiCharge fast chargers at all its North America assembly plants, Herman said.
Discuss in the Discussion Forums: Are you using fast chargers or slow chargers?