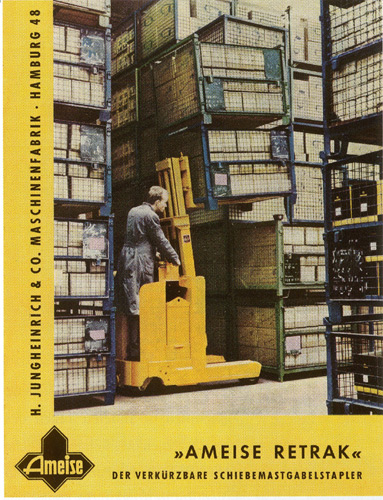 The "retrak" reach truck on a Jungheinrich (formerly known as Ameise) advertisement. |
IntroductionWarehouse operations consultant Dave Piasecki, based in Wisconsin, USA, writes in a web-published article titled
The Aisle Width Decision, that normal forklifts or standard counterbalanced forklifts generally operate in wide aisles, that is, aisles greater than 11 feet (3.35 metres) or 12 feet (3.65 metres) while narrow aisle forklifts, that is reach trucks, operate in aisles of eight feet to 10 feet (3.05 metres ). Last but not least very narrow aisles are the domain of man-order selectors and turret trucks, which operate in aisles less than six feet (1.82 metres) wide.
While narrow aisle forklifts or
reach trucks do not make up a large percentage of warehouse forklift sales, they play vital roles in stacking pallets and loading and unloading of trucks. Forkliftaction.com News reporter
Christine Liew speaks to two leading European manufacturers about their recent reach truck innovations.
Two claimsIn Jungheinrich AG's advertising material, the German forklift manufacturer, which makes its reach trucks in its Nordestedt plant near Hamburg, claims it invented the first reach truck. Linde Material Handling, which makes reach trucks at Linde Material Handling (UK)'s Basingstoke plant, also lays claim to being first with the reach truck. Despite the competing claims, the machines essential to modern warehousing operations, have been around for at least 50 years.
Jungheinrich founder Karl Friedrich Jungheinrich, whom
100 Years of Forklift Trucks, credits as the inventor of the stacker in 1946, is said to have invented the first Ameise "retrak" reach truck in 1956. In those days, Jungheinrich was known as Ameise.
Jungheinrich's Netherlands-based marketing officer Peter Trimp shed some light on the differing claims of the two German competitors when he revealed his company's claim was contentious. "To be honest, there is some debate about the theory. Some people say it wasn't Jungheinrich but another manufacturer that made a reach stacker before us but I have never seen it. In Jungheinrich it is common knowledge we were the first to build a reach truck."
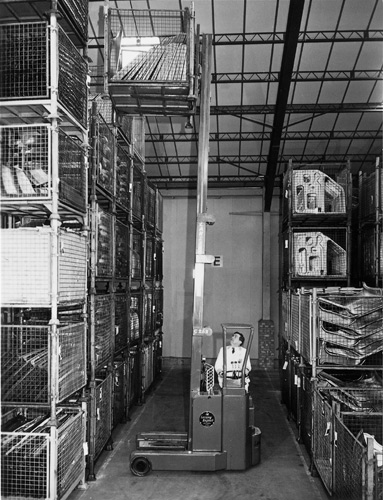 The first reach truck engineered at Lansing in Basingstoke, UK. |
Linde Material Handling's public relations officer Heike Oder told Forkliftaction.com News the first reach truck was invented in 1954 by the engineers of UK-based Lansing, which was acquired by the Linde group in 1989.
"It was an electric stand-on forklift reach truck with a mast that was retracted behind the front wheels and could be moved forward to reach into the aisles of a warehouse," she said.
An unconventional reach truckAt CeMAT 2005 in Hannover, Germany, this year, Jungheinrich presented a reach truck that could be used indoors and outdoors. Reach trucks are typically unsuitable for driving outside the warehouse but Jungheinrich's ETVC series are not typical.
"Normal reach trucks are not suited to driving outside. They can go over a ramp perhaps at most once a day but when you go over ramps again and again, there need to be adjustments to the trucks," Peter Trimp said.
Part of the reason the forklifts could work outside, was its "super elastic tyres" but the tyres also resulted in a compromise in the reach truck.
"A normal reach truck has really hard wheels, so the truck is very stable. But the C-version (ETVC series) has rubber tyres that are not as solid as a normal reach truck's tyres. Hence the C-version truck can't lift as high as a normal truck. The ETVC20 can lift up to 7,400mm (7.4 metres) while an ETV20 can lift up to almost 13,000mm (13 metres)," Trimp said.
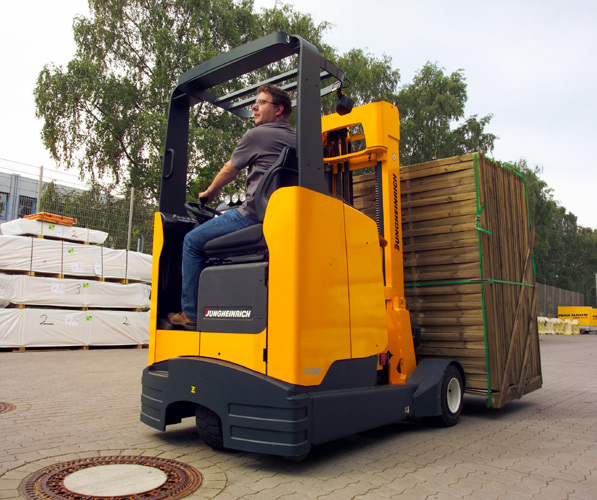 The Jungheinrich ETV C20 reach truck. |
The ETVC reach truck's lower lift height makes it appropriate for customers with small-to-medium-sized warehouses that would benefit from using the same truck to load and unload vans and trucks and stack pallets indoors.
"For larger warehouses that stack pallets higher [than 7,400mm], the C-version is unsuitable. Moreover, large warehouses in the Netherlands have loading docks so the trucks never go outside," Trimp said.
Customers of the C-version reach stackers include a Netherlands seed producer and an ink manufacturer, neither of which Trimp would name. The ETVC reach trucks are available in 1,600kg and 2,000kg load capacities.
360-degree steeringIn 2004, Jungheinrich introduced 360-degree steering, which could be beneficial for the larger warehouses by speeding up their operations.
"The 360-degree steering is an advantage because the driver can just turn the steering and he is already driving the other way. He doesn't need to slow down as much as with the 180-degree steering so it's much faster," Trimp said.
"With 180-degree steering he would have to brake and then accelerate again when changing direction.
"[However] you need larger space to use 360-degree steering but the difference in space measurement is not a lot. There are two modes to choose from now to use in different circumstances," he said.
The 360-degree steering would definitely be useful in loading and unloading trucks and vans. Although a key benefit of the ETVC reach stacker is the ability to use it outdoors for loading and unloading trucks, it does not come with the 360-degree steering mode. The 360-degree steering is currently available on the ETV 110-325 models. ETVC models were based on an old model reach truck with an old chassis.
Jungheinrich has no current plans to incorporate 360-degree steering on the C-version models but Trimp said it might happen in the future.
Linde puts battery below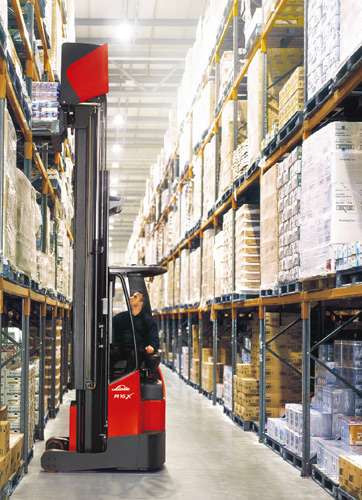 The new X range Linde reach truck. |
For Linde Material Handling, the basic design of its reach trucks had remained conventional for more than 50 years, until this year when Linde Material Handling (UK) developed what it says is a "new revolutionary truck design". The Linde X range was presented at CeMAT 2005 and Linde expects to gain market share from the new range.
Heike Oder told Forkliftaction.com News that Linde customers were primarily looking for "excellent ergonomics" in reach trucks, so it is not surprising that the new reach truck has been designed with operator comfort and safety in mind.
"High comfort and safety for the driver gives him the chance to be as productive as possible. Customers also look for high performance so load handling cycles can be executed much faster. Visibility and high stability of the mast plus fast battery changes are important too," Oder said.
The RX14-RX17 models with load capacities ranging from 1,400kg to 1,700kg have batteries located under the operator's seat and the mast permanently fixed to the chassis. The battery's new position allows the truck's designers to add operator comfort to the forklift.
The cab compartment is now twice as spacious leaving lots of elbowroom for the operator. The added space has made it possible for Linde to equip the truck with an extra wide full-suspension seat fitted with wide, adjustable armrests on both sides in which controls are integrated.
Linde says operator safety has been enhanced by moving the cab compartment inward to ensure the operator stays fully inside the truck at all times, with less exposure to injury.
The new mast design is also "inseparably associated" with the battery under the seat. The operator's seat is upraised and allows the operator improved visibility through the widely spaced mast uprights. In the new position, the operator sits closer to the mast and has a better view. The operator's view is not obstructed by hose lines, chains or hyrdraulic jacks.
Linde says the low-slung battery in a central position on the truck and the chassis-mounted mast add to the structural strength of the reach truck.
"The ballasting effect of the mast and the lower centre of gravity resulting from the position of the battery combine to give impressive stability and residual capacity throughout the load handling cycle. This adds more working precision and safety, improved further by minimal deflection of the mast that is noticeable when stacking or retrieving loads at heights of eight metres and more," a Linde statement said.
Linde claims the new mast design reduces up to 73 per cent of reach motions and increases productivity by 15 per cent, compared to conventional reach trucks.
The maximum lift height of the R14X is 9,500 mm (9.5 metres) while the R16X and R17X models can lift up to 11,500 mm (11.5 metres). The truck's maximum speed is 14km/h and it lifts loads at a maximum speed of 0.7m/s.
Sit-down or stand on?Most manufacturers cater for both the stand up and sit down operator position in their model line up. In USA and Japan, forklift operators typically used stand-on reach trucks, though factors like length of time spent operating and the need to get on and off the machine are reasons for this choice.
Trimp said while the first invented reach truck was a stand-on version, it was not a very ergonomic design.
"Ninety-nine per cent of all European reach trucks have seats. Only one per cent are stand-on and they are old reach trucks," he said.
Trimp made a guess at why other countries used stand-on reach trucks.
"In the US I heard there's a difference between drivers who sit and stand. Drivers who stand make less money than those who sit. It's more interesting for employers to get trucks where drivers don't have to sit on them."
Heike Oder said: "The design of Linde Material Handling reach trucks is basically the same all over the world but Linde MH does some market specific modifications."
Reach truck manufacturers around the world include Atlet, BT, Crown, Drexel, Yale, Hyster, Toyota and Kalmar.