Ask yourself these questions: Do I know where my forklift is? Do I know when my forklift needs its PM? How much is this forklift costing me? If you've answered "I don't know" to any of those questions, it's highly likely you need to implement a fleet and asset management system.
Melissa Barnett reports on what is available in fleet management technology and what it can do for your business.
According to the US-based Association of Equipment Management Professionals (AEMP), fleet management functions can include vehicle financing, maintenance and telematics (tracking and diagnostics), driver management, fuel management and health and safety management.
Three of the main challenges faced by forklift fleet managers, according to Jim Gaskell, director of global products for Crown Equipment, are "containing fleet costs, optimising operator and forklift productivity, and ensuring compliance with workplace regulations". Some might also include meeting environmental concerns. A 2007 study by Pennsylvania University showed companies can reduce their operating costs by up to 20% a year by using fleet management technology. The advantages of having a fleet management system in place seem to far outweigh the disadvantages, particularly in the current climate of economic rationalisation.
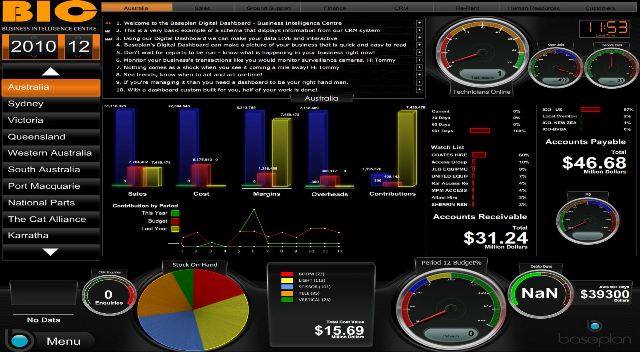 Baseplan data graphic |
At its most basic, fleet management technology operates at two levels. The first level gathers essential equipment information; the second analyses the information and makes recommendations based on the gathered information for a fleet manager to act on. "Collecting data generated at the most basic forklift level and analysing that information on a server can help managers optimise productivity and identify opportunities to eliminate inefficiencies associated with forklift fleet and operator management," Gaskell says.
Fleet management systems are essential for management service providers like UK dealer Barloworld Handling, which currently manage 25,000 forklifts annually across the UK. But, according to US management systems supplier ID Systems, no forklift fleet is too small to benefit from some type of data collection system and analysis, even if it is only managing driver identification and impact data. A forklift is a business asset and, like any asset, it needs to make a financial return whether it is one forklift or 25,000.
Collection and analysis ID PowerFleet |
Fleet management systems come in a bewildering range of options but basically it is a two-stage delivery. Equipment level data is gathered via onboard technology that interfaces with a central warehouse management system (WMS). The data is recorded in real time and a daily analysis of the information is sent to the fleet manager for action. The information is usually stored on the central server used by the forklift fleet's end-user or an out-sourced fleet management provider. Information is downloadable 24/7 to a smart phone, iPad or laptop or directly to in-van or in-workshop technology through a secure client portal. The amount of data that can be collected can be as simple or as detailed as required. All fleet and asset management systems offer a range of data parameters and management solutions but all of them should include several of the following:
- Tracking fuel consumption and operating hours;
- A pre-shift inspection checklist, a preventive maintenance management system, service hours, downtime analysis, automatically generated notices for up-coming training;
- Accident and collision documentation and prevention information, limiting access to authorised users through a keycard or terminal ID;
- A compliance solution that allows the system to record time spent on inspections and checks and compares it to defined standards and government regulations;
- Carbon emissions tracking;
- Tracking assets and their locations;
- Reduced paperwork and time spent by employees filling in forms;
- Total cost of ownership data;
- KPI reports; and
- "Right-sizing" of fleet equipment reports. According to Debbie Tworek, spokesperson for US dealer Associated Solutions, reducing just one forklift would conservatively save more than $30,000 a year in labour and other operational costs. For the price of one hour of labour or a single scheduled maintenance visit, your company could receive a full year of fleet management.
Only 20% of forklift fleet costs relate to the initial equipment purchase. The remaining 80% is directly tied to maintenance, administration and utilisation, so it makes good economic sense to implement a fleet management system that can capture long-term data so informed decisions can be made on equipment investment, developing suitable work programs and improving day-to-day operations.
The majority of fleet and asset management systems can be implemented in 30 to 60 days; initial set-up need not be expensive. Out-of-the-box devices are available from most system suppliers, for example, ID Systems' PowerBox is pre-configured and employs universal hardware and automated set-up, enabling fast installation. It can be attached to all forklift types and bought on a monthly subscription with no upfront capital outlay. Companies need to be aware that out-of-the-box solutions may not address all their operational parameters and a bespoke solution might be better for a comprehensive overview of their asset and fleet management requirements.
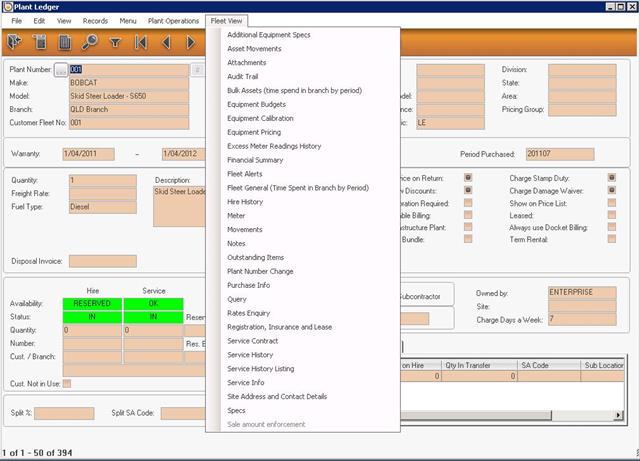 Baseplan fleet management page |
Fleet management systems are expected to be in place for several years so, to ensure a company gets the best value from the system it is buying, there are few things that need to be addressed before implementation. They include: having relevant asset costs and utilisation data available; ensuring operational needs have been well thought out in advance; and that staff will be adequately trained and accept their role in managing the system. When Australian company Baseplan implemented Linde Materials Handling Australia's fleet technology it ensured key management staff were kept actively involved. Involving "super-users", says Nigel Hammond, Baseplan's business development manager, allowed Linde to keep implementation costs down and become self-sufficient and independent very quickly.
Jason Bratten, vice-president of BEB Industrial Asset Management, a US-based independent software provider, agrees and believes the client should be heavily involved in implementation. BEB creates a "corporate tree" for clients early in the software development stage that customises the business structure geographically or by product or to whatever structure the client uses. The structure informs software engineers of what assets the company has, where and what they are doing. The client account manager then audits the site survey data before entering it into the system. Paul Dolby, of independent provider Chevin Fleet Solutions, believes in-house data management and analysis is best because there are significant benefits to retaining control of current and historical information, especially when you need impartial answers.
However, not all companies wish is manage their fleets in-house. According to Tworek, most companies decide to outsource because they simply don't have the time to gather or analyse fleet information in-house. "Even if customers receive reports they are often challenged to read, digest and convert the data into actionable objectives," she says. Having an outside resource consistently providing cost-saving insights has proven justifiable to many clients. Bruno Cipriano, logistics manager for Portuguese food and beverage company Sumol+Compal, believes outsourcing has given his company better, faster access to technological upgrades and minimal downtime when upgrading forklift fleets, but its major benefit, he says, is a rapid response to maintenance issues.
Detailed telemetry or simple monitoring tools - you choose Whether a company decides on a sophisticated or simple fleet and asset management system largely depends on budget and operational requirements. Any sized forklift fleet can benefit from collecting the most basic data, but software developers, suppliers and end-users all agree it is what you do with the information once gathered that is the most important part of the process. Part of the problem in the past was that companies were confused about what type of data they should collect. AEMP believes it has come some way to resolving that issue by designing an industry telematics standard. AEMP's Telematics Data Standard V1.1 was designed by industry professionals and released in late 2010. The standard is designed to allow end-users to integrate key telematics, such as operating hours, location, fuel consumption and odometer readings, into their existing fleet management reporting systems using a standardised XML format, which allows the end-user to use one program to retrieve data from any participating telematics provider. The standard is currently being trialled in the construction sector.
Several forklift manufacturers have developed their own fleet management systems. Hyster's management system, ForkTrack, incorporates features such as pre-start safety checklists, driver ID controls, driver restraint controls, transmission controls, impact detection, integrated digital weight indicators and built-in safety alarms for overloads, speeding and proximity. Equipment data is collected in real time and transferred by wireless link to an office computer where analysis takes place. Analysis fields include safety, fleet, operator compliance, asset management and service information.
UK equipment dealer Barloworld offers a fleet management service that uses BTD, a telemetry device developed by Barlowworld to work in conjunction with Hyster's onboard Canbus system to capture live performance data. BTD can be fitted to all types of forklifts and other handling equipment. The fleet management system reports back with performance information on each truck, including run time, hour-meter readings, impacts, maintenance completion and cost of ownership.
ID Systems has partnered with Raymond Corporation to use ID's PowerFleet as part of its iWarehouse fleet optimisation system. The PowerFleet vehicle management system (VMS) works with similar parameters to other systems but can schedule maintenance according to actual vehicle usage rather than by calendar or manual data entry.
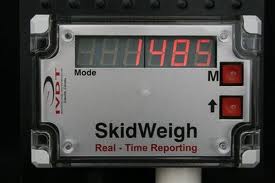 skidweigh ED2-400 |
The ED2-400 Series SkidWeigh system is advertised as the only system that measures a forklift's true operational usage pattern and provides the client with utilisation reporting in real time. The information, according to Ted Jurca, president of the US-based company, is updated every second and uses comparisons between actual and desired forklift operating activity to send warnings to the operator of under-utilisation.
Nigel Hammond says Baseplan's IVT (in-van technology) solution is its most popular fleet management system. IVT has been used by Linde Material Handling Australia with impressive results. Linde saw an increase in job productivity from 2.4 service jobs per day per technician to 3.2 within six months of implementing IVT.
BEB's Meter Activity Technology (MATT) is an onboard tracking unit which transmits forklift meter data directly to a BEB receiving unit. According to Bratton, BEB's MATT system can save a fleet of 40 forklifts up to 50 PM's a year equating to a cost saving of USD5,000 (AUD4,769) a year. By having the data the forklift fleet can be reduced by two forklifts for a saving of approximately USD12,000 (AUD11,445) annually on ownership and operating costs.
UK-based Transmon Engineering's latest LCD version of its TDS5 fleet management system provides a highly detailed daily check procedure that disables a forklift's engine ignition until every question has been answered by the operator. Paul Sercombe, sales director for Transmon, says: "Not every forklift is the same, so it is important for the daily checklist to be customised to suit the equipment and its application."
As with all technology, advances are being made at an alarmingly rapid rate. Rush Tracking Systems, a US-based RFID solutions provider, has released Orchestra, a software module for use with its VisiblEdge and other warehouse management systems (WMS) to provide more detailed analysis of warehouse workflows and procedures. For example, RFID-enabled forklifts will generally tell the WMS everything a forklift is doing, risking errors in analysis. Orchestrator software intervenes in the process, providing more detailed information to the WMS and avoiding response errors from the system.
In the past few years, fleet management systems have taken a large slice of the software industry's interest. It is a rapidly changing field that no one with equipment can afford not to play on. "Fleet management systems have the potential to unify globally dispersed business operations by limitlessly joining internal departments, customers and suppliers. They offer businesses highly valuable consistency that can equal big financial benefits," Chevin Fleet Solutions' Dolby says. "Having a central repository for the critical operational data is becoming a must have, rather a nice to have."