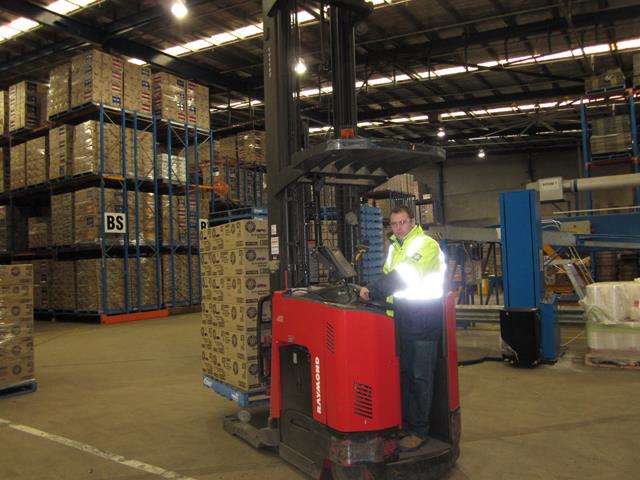 The initiative has set a clear standard of operating expectations and drivers are held accountable to this standard. PHOTO: SMITH'S SNACKFOOD COMPANY |
After concerns were raised about inconsistent and unsafe forklift operation at its Dandenong warehouse, food supplier The Smith's Snackfood Company researched and implemented a new safety initiative which is now in the running to win a Victorian WorkSafe Award for best solution to a workplace health and safety issue.
The initiative, called Forking Great, involved behavioural education, workplace changes and competency-based training and reinforcement.
Health and safety manager Marissa Meyers tells
Forkliftaction.com News that the company employs around 50 forklift drivers in shifts at the company which operates 24 hours a day, six days a week.
Around eight reach trucks units are in use along with three counterbalance forklifts.
"We brought in a trainer to assess all our forklift drivers and provide input into best practice in the industry," says Meyers, adding that re-educating drivers was the real focus.
The major issues identified at the warehouse included racking damage, speeding concerns, and traffic management of forklifts and pedestrians.
Over a four-month period, the initiative resulted in a final set of 15 forklift rules which provide a consistent, safe and accepted method of forklift operation.
While the rules are not a new way of operating forklifts, they require forklift operators to work in the same manner in which they would for a forklift license assessment.
"It has been new for many staff as poor practices had become common place and there was not a set standard of excellence," says Meyers.
"Forking Great has changed this by setting a clear standard of operating expectations and drivers are held accountable to this standard."
She adds that the initiative has increased the amount of reporting on unsafe behaviours and near misses in relation to forklifts.
"This has had a positive impact on the safety culture on site by raising the level of safety awareness and accountability for all operators.
"We also have objective competency assessments from a qualified forklift trainer for all staff so we have confidence in the skills and knowledge of our operators."