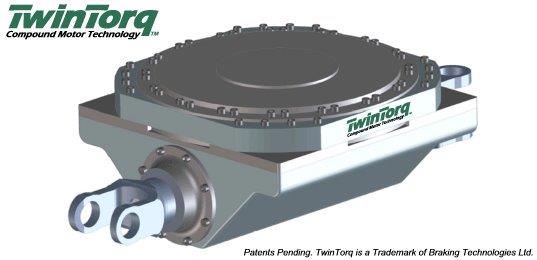 TwinTorq compound motor |
KersTech Vehicle Systems is making headway toward
development of a TwinTorq motor suitable for forklifts and other vehicles with frequent start-stop drive cycles.
The motor improves battery energy efficiently and significantly extends driving range because each stop and start is a recovery event, says Lester Erlston, chief executive officer of the Beaverton-based business. The motor combines electric and hydraulic torque technologies to extend operational runtime.
A TwinTorq prototype being built at the Oregon Institute of Technology in Klamath Falls incorporates "critical control algorithms", Erlston says.
"Forklift warehouse drive cycles are ideal for TwinTorq motor systems," he says. "We see tremendous opportunities for that." Other potential markets include city and shuttle buses, refuse and parcel trucks and port handling equipment.
KersTech has received project hardware and software funding of about USD459,000, largely from the Transportation Research and Education Centre at Portland State University, trade association Drive Oregon of Portland, independent Oregon Built Environment & Sustainable Technologies Center Inc, the City of Portland Development Commission and forklift manufacturer Hyster-Yale Materials Handling Inc.
KersTech intends during 2015 to integrate the custom-built TwinTorq prototype motor into a 3 T Hyster forklift for trials at the Fairview, Oregon research and test facility of the Nacco Materials Handling Group Inc subsidiary of publicly traded Hyster-Yale. The Mayfield Heights, Ohio-based forklift maker's commitment includes a USD40,000 contribution of in-kind services.
KersTech filed in 2013 for US and international patent protection on the technology in the motor system.
KersTech received notice in March of a US patent allowance for the gearbox structure of the TwinTorq drive system. Erlston says the application for that patent was filed five years ago.