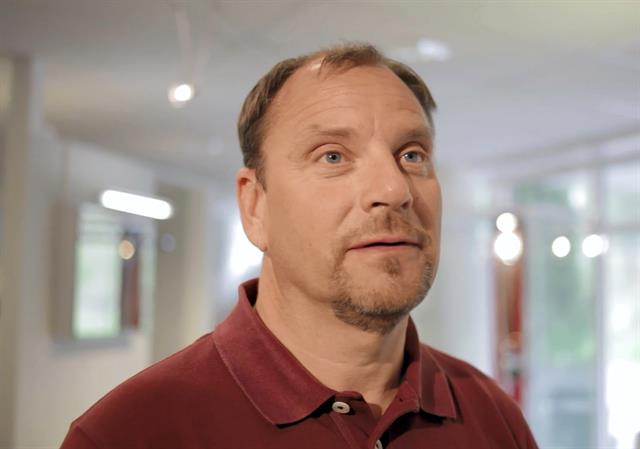 Karl-Eric Wikström, IDO's Technical Manager. |
IDO was chosen as a pilot customer for Rocla's new automation innovation Rocla Route Optimizer route optimizer. With the new software IDO was able to increase their existing transport capacity with 15%. IDO has been using Rocla's automation solution in their sanitary ware production since 2012.IDO is a Finnish producer of sanitary ware. Besides Finland the company operates in other Nordic countries and in the Baltics. IDO is a part of Geberit Group. IDO chose Rocla's automation system in 2012 to their modern ceramics factory.
"We had contacts with other suppliers also but we know Rocla from the past as a reliable supplier. We wanted a local supplier from whom we can get full support, 24 hour 7 days a week. Rocla is a big player in the market so we felt very comfortable with that choice", tells Karl-Eric Wikström, IDO's Technical Manager.
Productivity and safety increased with automationWhen considering automation for their production site IDO had two main criteria: maximizing the production flow and the need to get rid of heavy manual work.
"Our ceramic products are quite heavy to handle manually. We need to keep material flow constant and keep the product unit cost as low as possible. Of course the personnel costs play an important role in high cost country such as Finland," explains Mr. Wikström.
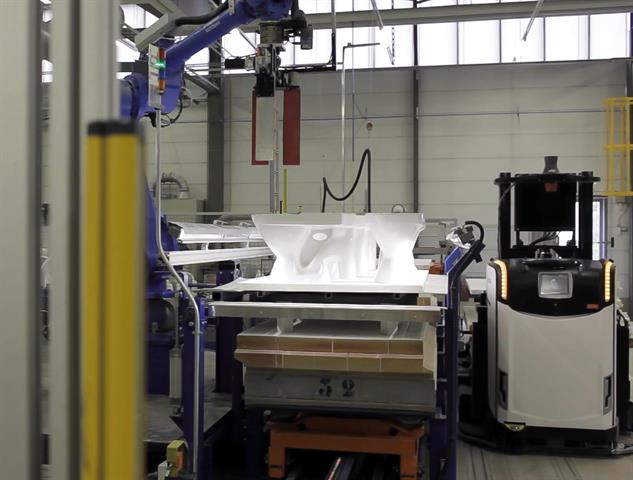 Rocla Route Optimizer was implemented during normal production |
"
Rocla's AGVs are programmed so that it is easy to get the products and the production flow forward. Earlier with manual operation when we moved the product from one production cell to another, there was always a man on a manual forklift and he should look at the production flow and follow up the production units. Now with AGVs you get the information in between the production cells and AGV transport system automatically. That's why it's easier to get the production flow constant and moving forward continuously," explains Mr. Wikström.
"Also the AGV system has helped us to have firing oven up and running all the time. This is a crucial phase in the process to have products ready all the time for the oven because we cannot stop the firing process. Rocla's WMS system helps us with this, so we have better control on the raw material feed to oven. WMS is a very good system to have also full control of where we have the pieces in the factory. It's easy to use and you can change the control of the AGVs via the WMS if you choose to change the flow somehow in the factory," Mr. Wikström continues.
Safety of the system was also main criteria when choosing Rocla's automation solution. Rocla AGVs work in same area where personnel is working, so safety for personnel as well as safety for transported goods is essential.
"We are producing ceramics that themselves are fragile. It's very easy with the AGV system to control all the speed and lifting. You will not have any cracked pieces in the production," says Mr. Wikström.
"Rocla's automation project itself went very well, we got exactly what we wanted technically and it was on time. Now after a few years of operation we are very happy with the installation and the people in production are very pleased with the system. I would recommend Rocla's automation solution for production units who have a big factory with long distances and constant production flow," concludes Mr. Wikström.
Rocla Route Optimizer's implementation in 2016 to existing automation systemIDO was chosen as a pilot customer for
Rocla's new automation innovation, Rocla Route Optimizer early 2016. With this unique, patent pending solution Rocla boosts its automation customers' material handling up to 20%. The solution optimizes the routes AGVs use in customer sites so that traffic flow is always smooth without interruptions.
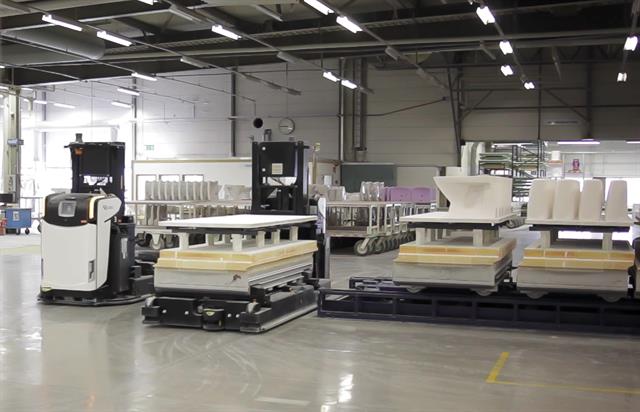 AGVs do more but drive less |
Since
Rocla Route Optimizer dynamically finds the fastest routes for each AGV, there is no need for manual traffic rules anymore. You can say goodbye to traffic jams. Software's game-changing ability to make instant decisions on better routes enables constant operation of the vehicles. As a result, you need fewer AGVs for a given task and achieve savings in both loaded and empty driving. The AGVs do more but drive less. For customers this means improved efficiency and reliability in their logistic process.
With the new Rocla Route Optimizer software the design and ramp up of a new system is much easier and faster to accomplish. Flexibility increases tremendously thanks to new solution: you can increase transportation capacity in existing systems, which reduces total cost of ownership (TCO) of the vehicles. It is also easy to add or reduce vehicles in an operation.
With the new software IDO was able to increase their existing transport capacity with 15%."The new innovation Rocla Route Optimizer did not require any changes physically in our production. The AGVs are exactly the same and also the drop and pick points are the same. This was implemented during normal production. The complete process was in the hands of Rocla engineers, so it went very smoothly. This new software is more intelligent and we have a benefit of 15 % more capacity. First of all we have to say thank you to Rocla for choosing us a pilot plant, we are very pleased with that. It is very nice to see the AGVs driving around more smoothly and in a more clever way", explains Mr. Wikström smiling happily.
Rocla OyAGV International SalesP: +358 20 778 1332E: send an emailW: website