More than 20 years after it first entered the manufacturing lexicon, lean thinking is finally taking hold in the warehouse and DC. The last frontier for lean implementation is the industrial battery room.But is lean thinking needed in the battery room? Is lean implementation even possible? And if so, is it worth spending the time, money and resources to accomplish it?
Lean's foundations are in Henry Ford's mass assembly manufacturing system, developed in the early 20th century, and the Toyota Production System (TPS), created in the mid-20th century. In its simplest form, lean manufacturing means producing goods with less; it applies fewer resources without affecting the quality or quantity of the goods produced. Toyota's purpose in developing its system was the elimination of waste, and TPS is focused on seven sources of waste:
Overproduction - manufacturing items before they are required
Motion - unnecessary motion caused by poor processes
Waiting - leaving goods in stasis before they are ready for the next process
Transportation - excessive movement and handling to get goods from one process to the next
Over-processing - effort that adds no value to the finished product
Inventory - excess material or equipment that ties up money that could be used for other things
Defects - allowing quality deficiencies that result in rework or scrap
One reason for the delayed implementation of lean thinking in the warehouse is that the original concept was designed for mass produced items. In the warehouse, volumes aren't huge and are not standardized, so the science of lean can't be applied in exactly the same way.
To produce more with less - and with less waste - in the warehouse, managers can design storage areas, cross-docking systems, pick systems and shipping areas to function faster, with less energy and fewer labor hours just as easily as can be done in a manufacturing line.
With lean thinking becoming a powerful management tool in the warehouse, why not in the battery room? Battery room activities are often seen as ancillary to the warehouse's main business of storing and distributing, as a result, the problems in the battery room are often considered insignificant. These beliefs are based on a lack of understanding about the magnitude of waste in the typical battery room.
When battery room activities are studied, it quickly becomes apparent that six types of waste exist there.
Transportation: Unnecessary trips to the battery room to change batteries.
Inventory: More batteries and chargers in the fleet than required.
Motion: Battery changing and watering processes that require extraneous movement.
People: Too many people watering and charging batteries.
Waiting: Operators queuing for battery changes due to poor charging practices and slow watering.
Defects: Operator selection of the wrong battery and/or incorrect watering.
Studies show that waste in the battery room can cost large warehouses and DCs hundreds of thousands per year. Even small operations with as few as 10 to 20 forklift trucks can lose tens of thousands due to this wastage.
So, how does one eliminate waste in the battery room? Today's batteries are the best ever and with proper maintenance will provide years of use. To maximize a battery's life, managers should understand six areas of battery maintenance and use:
Charging: Batteries should be fully charged and allowed to cool down before use.
Discharging: Batteries should be fully discharged, as partial discharges increase the number of cycles and decrease operator productivity.
Cycling: Under-cycling batteries creates corrosion even when batteries are not being used. Over-cycling, gives batteries inadequate time to cool down, which causes corrosion through increased heat.
Watering: Under-watering a battery exposes the plates to air, which reduces capacity. Over-watering can cause boil over.
Cables and Connectors: Broken cable and connectors must be repaired.
Washing: Regular washing minimizes short circuits across the surface of the battery, reduces energy loss and minimizes tray corrosion.
To achieve measurable and sustainable elimination of waste, managers should focus on the three major impacts on battery room operation and maintenance:
Rotation, Rightsizing and Watering.RotationThe #1 cause of reduced battery run time, reduced battery life and waste is improper battery rotation. Left to their own devices, operators will take the closest battery (in order to make the quickest change) or the newest battery (in hopes of getting the longest run-time). This is despite the fact that the correct battery - the battery that has had the longest cool down time since charging - may be in the back of the battery room.
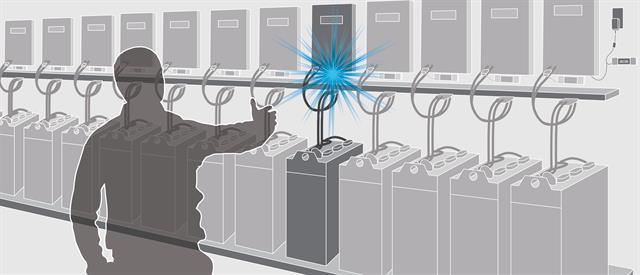 iBOS ensures proper rotation. |
The key to ensuring proper rotation is to make picking the right battery simple. When proper battery rotation practices are implemented the results are dramatic. In a study of one company's introduction of good rotation practices the average battery run time increased from 6 hours 30 minutes to 6 hours 57 minutes - nearly half an hour.
Battery organizing systems are the most effective tool for ensuring proper battery rotation. The Philadelphia Scientific iBOS
® (intelligent battery organizing system) monitors all batteries in a pool and eliminates operator error by determining which battery has had the longest cooling time since charging.
iBOS animated demonstration
Once charged, each battery is placed in a queue. The simple display tells the operator which battery to take and an alarm sounds if the wrong one is taken. In addition, the battery room manager can monitor all the essential battery room information online.
RightsizingRightsizing a battery room offers significant potential cost savings by matching the size of the battery fleet to the needs of the forklift fleet. However, determining the proper size battery fleet can be a challenge because of the difficulty in obtaining accurate information.
Operators, while using the batteries and accessing the battery room every day, may provide unreliable feedback and industry "standard" ratios assume all facilities operate in the same way, and do not account for changes in warehouse and battery room operations over time.
The lean method for rightsizing a battery fleet requires ongoing operations feedback and measurement. Key areas to measure include battery availability, including when there are more batteries than needed and when the battery room is running out of available batteries; the length of cool down time; and battery cycles per week.
Rightsizing via the InternetWhen combined with the power and accessibility of the Internet, battery organizing systems are the ideal tool for rightsizing battery fleets. For example, users of iBOS can subscribe to the iBOSWorld™ Web Service, which enables managers to optimize assets by analyzing performance and creating reports remotely.
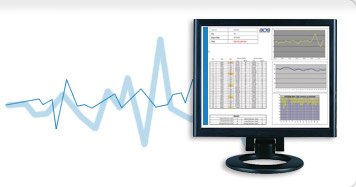 Battery Room Reports via the Internet |
|
Battery wateringWatering industrial batteries has been called "a simple job done poorly," there are only two steps in the process: Determining which batteries need watering and watering them.
But each of these steps is fraught with potential pitfalls. In many warehouses, batteries are watered on a set weekly schedule. Not only can this be a complicated procedure, but also a time waster, as many of the batteries that are checked don't need watering - and many that are checked needed watering earlier.
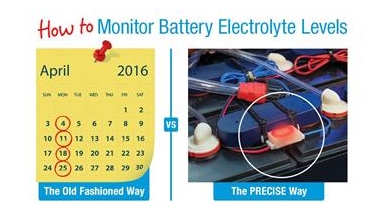 Old Fashioned vs Precise Battery Watering |
|
Using technology to determine the scheduleThe most effective way to determine when batteries need watering is with a battery watering monitor. Monitors, such as the Philadelphia Scientific Blinky
™, allow watering on an as-needed basis instead of an unreliable schedule.
Watering batteries quickly and preciselyPrecise watering of batteries is critical: Over-watering can cause boil overs and decreases the battery's useful life because sulfates are washed out. For every boil over, the battery loses approximately 3 percent of its capacity and in time, boil overs can decrease the life of a battery by six months or more.
Under-watering happens when batteries aren't watered when required. When a battery's positive and negative plates dry out capacity is decreased, even when water is re-introduced the battery will not return to its previous performance. In the worst case, a damaged cell needs to be replaced.
The quickest and most reliable way to water a battery is with the Philadelphia Scientific Water Injector System™ with precision level-sensing valves. The Injectors are installed into each cell on a battery, and tubing runs through each Injector, forming a single, continuous flow path. The operator clicks on a water hose, opens a valve and can water a battery in 15 seconds or less - a fraction of the time it takes by hand and up to eight times faster than other systems.
Watering system comparison
The Lean Battery RoomThe warehouse and DC battery room are the last frontier for the implementation of lean practices. Yet the Lean Battery Room can be implemented immediately with existing technologies and proper maintenance and operating practices. The potential benefits are enormous, representing tens of thousands of dollars in savings from reduced waste even in small- to mid-sized battery rooms.
Visit
www.phlsci.com for information about the technology available to Lean your Battery Room.
For more information on Lean Battery Rooms
send an email to Chris to receive the
'Lean Battery Room - Best Practice Manual' and
'Lean Thinking Comes to Battery Room'.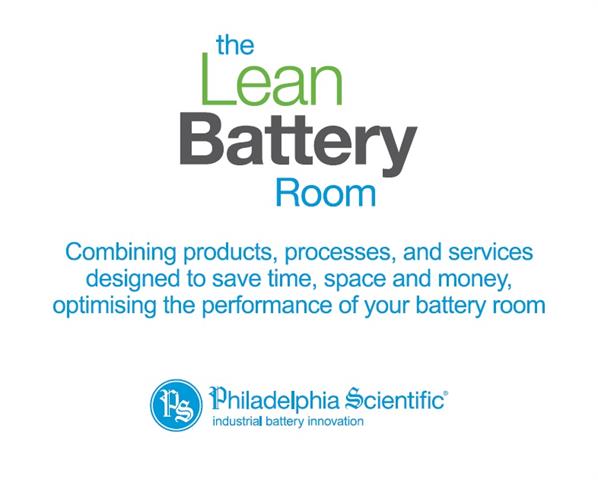 Lean Battery Room - Do more with less. |
|