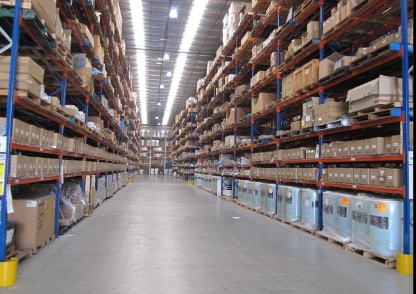 Cache's new Wacol warehouse |
What is a lean warehouse, how is it achieved and what tools can be used to make your warehouse lean?
Melissa Barnett looks at the theories behind lean thinking and some of the ways in which modern warehousing brings theory and practice together.
It has been 20 years since James Womack and Daniel Jones published their ideas on management systems in their book
Lean Thinking: Banish Waste and Create Wealth. Although lean thinking was not a completely new concept at the time, Womack and Jones' theories were considered revolutionary and coined the name for a new way of thinking in regards to manufacturing models. Initially written in anticipation of a worldwide manufacturing recession which didn't materialise, Womack and Jones analysed the highly successful manufacturing model of the Toyota Corporation and expanded upon it in an attempt to recession-proof manufacturing companies, by streamlining their processes and eliminating unnecessary waste, and to sustain financial growth, by aligning customer needs and satisfaction with employee engagement.
The Toyota Production System (TPS) is still used by Toyota and essentially follows the philosophy of Jidoka - automation which stops when a problem occurs, thereby reducing the chance of a defective product, and Just-in-Time (JIT) - where each process produces only what is needed by the next process in a continuous flow. Each process is designed to eliminate waste. Bill Pedriana, director of sales and marketing for US manufacturer Big Joe Forklifts, says that his company has always been an advocate of lean thinking. "While the methods and vernacular of lean principles have evolved over the years, many of the core concepts remain important. Regardless of the amount of technology employed, the flexibility, nimbleness and ease of deployment of labour remains a key ingredient in driving efficiency in operations," he explains.
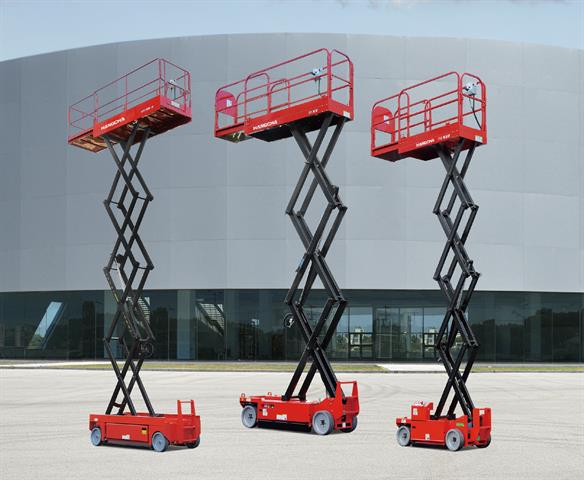 Hangcha Scissorlifts make warehouse picking more efficient |
Through the identification of waste and wasteful processes by both employees and management, the optimal product will be delivered and the optimal workplace environment should be achieved. According to both the Toyota Production System and Womack and Jones, the pursuit of this optimisation needs to be continuous to be sustainable.
Over time, lean methodology has expanded beyond manufacturing to cover a multitude of business systems from supply chain management to health care. Warehousing has been a natural fit for lean thinking because at the core of every good warehouse is the desire for efficiency in economies, value, time, people and space.
Theory + practiceThe principles of lean thinking, whether espoused by Henry Ford, Toyota, Womack and Jones or one of the other proponents, basically embrace the following:
Specify what creates value from the customer's perspective. According to Pedriana, the key to unleashing the power of lean principles in a rapidly changing world is to know what your value is to your customers and optimising for that above all else to meet needs and exceed expectations.
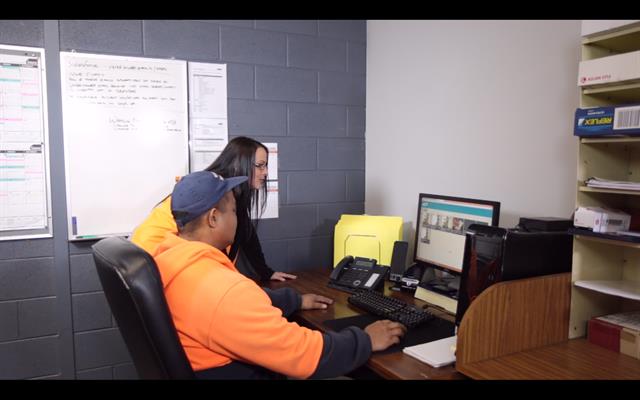 Ausfork in-house training program |
Identify all steps across the entire value stream and identify the actions that add value to your project/product. Standardisation of steps means that you create a baseline from which improvements can be sustained. This is done through the workforce 'culture'. It is humans who identify problems and create sustainable solutions, who create a culture of problem solvers. Warehouses contain any number of operations where things can go wrong, and quickly - resulting in damage to goods, infrastructure, equipment and, sometimes, operators. Daryl Lord of Australian-based equipment training company Ausfork says that product and infrastructure damage in warehousing costs millions each year, with the human implications and costs even more significant. Lord suggests that warehouse managers and employees refresh their equipment training regularly for a number of reasons: to keep compliant with Workplace, Health and Safety regulations, but also to ensure that operators have a base standard of operation and can recognise dangerous habits and make appropriate changes before damage/waste occurs.
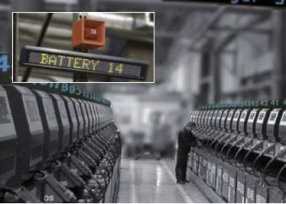 Philadelphia Scientific's Battery management system |
Create value flow - a consistent flow of steps that always produces good results. Ensure that the workforce understands the internal and external flow of goods. Is there the right quantity, at the right place, time and quality? However, the optimal flow of goods is not the only important flow required in the warehouse. Chris Parkinson, spokesman for battery specialist Philadelphia Scientific, also believes that understanding the optimisation and flow use of warehouse equipment is just as vital. In a white paper, Philadelphia Scientific's vice-president of sales and marketing, Harold A. Vanasse, indicates a number of the sources of waste identified in the Toyota Production System as also common in a warehouse battery room. These include wasteful trips to chargers, storing more batteries than actually required, misunderstanding by operators of battery maintenance practices and incorrect selection of the right battery. Operator error and subsequent waste of time and money, says Parkinson, can be mitigated by an appropriate management system such as Philadephia Scientific's iBOS battery management system. "Ultimately, if operations underspecify equipment or leave out essential items, such as management systems and monitoring technology, they will pay above and beyond the cost of the 'extra' equipment through additional operational costs and the ongoing expense of repairs and replacements," he suggests.
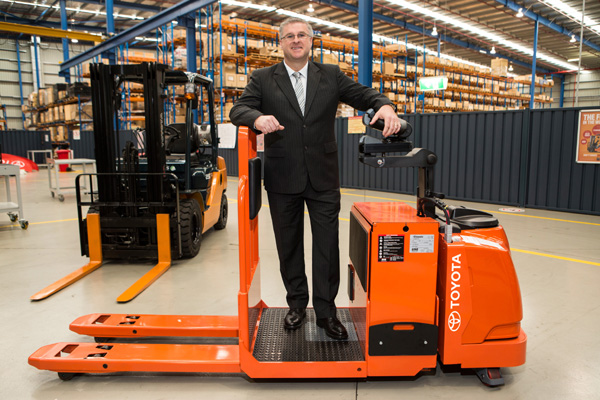 Lencrow can find the right mix of warehouse equipment for a lean warehouse operation |
Only make what is pulled for the customer - just-in-time. JIT is a core tenet of the Toyota Production System and lean thinking in general. When applied to warehousing, JIT can mean "only pull what is needed by the customer"'. Warehouse floor design and material flow based on stability as opposed to gross volume (i.e. identifying what items are picked frequently rather than in large volume) are essential for a lean warehouse. It has been suggested that up to 60% of most manufacturing operations add no value to the product and are, therefore, 'waste'. This could also be said of warehouse operations. In addition, says Ross Grassick, CEO of Australian forklift dealer Lencrow, the cost of warehouse space being at an all-time high means that customers are wanting to put as much in the warehouse as they can as well as reducing handling times. "The first step in efficiency is to work out how much you need to fit in and the cycle time that the goods are to be stored and then dispatched. The correct mix of racking, materials handling equipment and management system can improve efficiency by up to 50%," he says.
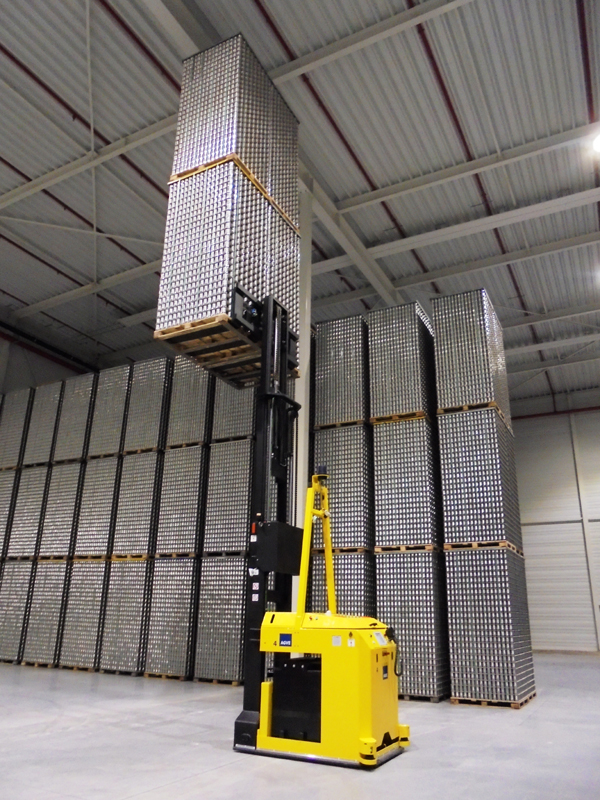 AGV Solutions A8-4 pallets |
Mats Herrstromer, president of AGV Solutions based in Charlotte, Carolina, USA, believes that an automated guidance vehicle (AGV) system sees a quick return on investment, typically in the two- to three-year range, due to reduced labour costs and improved safety. He says AGVs can operate 24/7/365, so there is no down-time or loss of production cycle time. They have a perfect product-tracking record and the load never gets lost. Furthermore, an AGV will reduce damage costs to material and facility. "We have a customer in the printing industry that tracked their waste and damaged paper (and) the AGV system significantly reduced waste in both raw material and finished product. The installation of an AGV system is often the catalyst to improving business practices and material flow. Reviewing the complete material flow often unearths opportunities to improve the complete operation or free up floor space that can be used for something more productive."
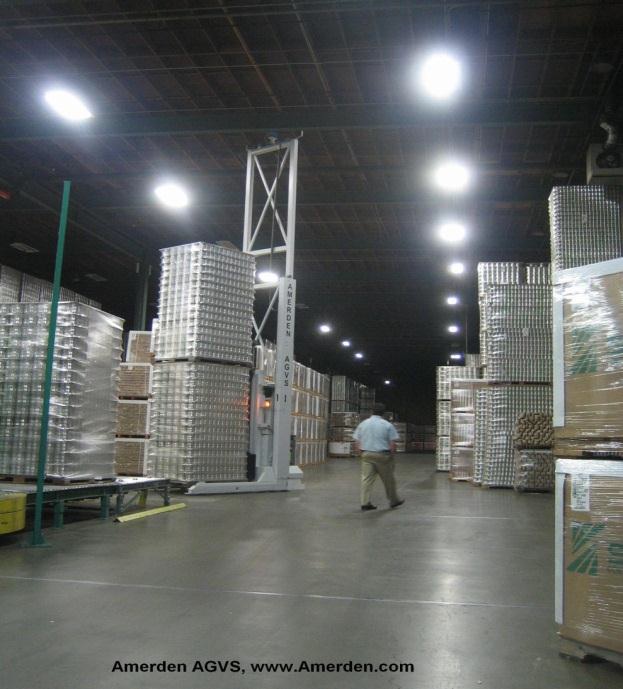 Amerden's space-saving AGVs can stack four high |
Roland Anderson of US AGV manufacturer Amerden agrees that AGV systems improve transport efficiency and increase storage density. One of Amerden's customers, a packaging manufacturer, needed to improve the transport efficiency of its finished product between manufacturing and warehouse and, in addition, wanted to increase storage density without modifying the facility. Amerden custom designed an AGV system that could carry the finished loads stacked 2.6 m high. The AGV then stacks the load four high in 160 lanes and across 2,300 floor locations,so reducing valuable wasted space. The system uses two laser guided fork vehicles guided by automatic laser at ceiling height. The vehicles efficiently link six production pick-up locations with one centralised stretch-wrapping machine and then the warehouse. The whole operation runs 24/7. Anderson adds that although the AGV system's cycle time is slightly longer than a forklift's due to, lower speeds it is safer, more consistent and is more efficient at handling the finished product.
Jussi Ali-Löytty of Finnish AGV manufacturer Rocla, believes that automating routine logistics transport and warehousing means that "customers are able to utilise personnel resources more intelligently in generating value-adding to their business chain". Ali-Löytty says on its own manufacturing floor, Rocla's decision to introduce modular AGV platforms with software meant that the company was able to move from customised design and production to full industrial production, significantly reducing design times, increasing production times and maximising quality to record levels. Ali-Löytty adds that using a traffic optimisation system, such as Rocla's LogIQ can increase the efficiency of a customer's warehouse system by up to 20%. The LogIQ solution optimises the routes AGVs use in customer sites by dynamically finding the fastest route for each AGV. This means that traffic flow is smooth and uninterrupted resulting in improved efficiency and reliability in the logistics chain.
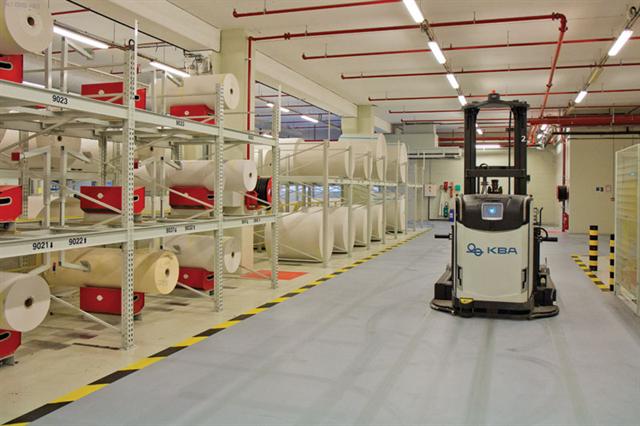 Rocla AGVs at work |
Strive for perfection by continually removing successive layers of waste - sustaining change. Incorporating the PDCA (plan, do, check, act) cycle helps identify and eliminate waste. Ask the questions: What is today's plan and how do we measure today's performance? Pedriana believes that many tasks and processes have changed in the supply chain due to technology. "We still have a long way to go to maximise the value that people can contribute in the workplace. Whether the need is the transport of materials, work positioning, or enhancing access to materials, we are not done coming up with ways to get more done with less," he says.
To create a lean warehouse, you must have not only the appropriate tools and methods, but you have to create a culture where each employee is able to solve problems. Grassick suggests that every warehouse should have realistic production targets and goals. Smart, specific, measurable, attainable, relevant and timely goals should be applied to each department and role in the operation towards the overall goal. An operation, he says, is only as strong as its weakest link and goals and productivity should be monitored and amended regularly.
Pedriana says looking at basic input/output cycle times is also very important, but it is equally important to look at their outcomes over time. It seems in the pursuit of profit that organisations often place an inordinate amount of focus on speed. "Speed is easy to measure, so it tends to get measured and championed as a metric a lot. How many cases or lines per hour versus error rate is a good example. At Big Joe, we look at things a bit differently: As there is one metric involving speed that dominates all others, the speed of companies to effectively manage change in their operations to meet the needs of their customers. This may be the most important cycle time of all, and a place that lean principles can also be applied. Lean principles are fairly straightforward when optimising what can be predicted, but with the right perspective they can also be utilised to improve the adaptive capacity of processes and systems," he explains.
The world's manufacturing and warehousing sectors have recently been through the biggest recession since the 1930s. If we have to face such circumstances again, implementing a business model such as lean thinking may not be the only answer to recession-proofing your business, but it certainly makes sense to give it a go.
Additional information by our contributors:LENCROW: website
PINPOINT HANDLING WASTAGE IN YOUR WAREHOUSE------------------------------------
HANGCHA: website
HANGCHA NEW SELF-PROPELLED ELECTRIC SCISSOR LIFTING PLATFORM-----------------------------------
ROCLA: website
IDO'S TRANSPORT CAPACITY INCREASED BY 15% WITH ROCLA LOGIQ ROUTE OPTIMIZER------------------------------------
AMERDEN: website
AGV SYSTEM: INNOVATIONS FOR WAREHOUSING------------------------------------
PHILADELPHIA SCIENTIFIC: website
LEAN WAREHOUSE -->LEAN BATTERY ROOM------------------------------------
DOUGLAS BATTERY™: website
DOUGLAS BATTERY™INTRODUCES THE LEGAC2™ MODULAR CHARGERSAnd Special Thanks:BIG JOE: website------------------------------------
AUSFORK: website------------------------------------
AGV SOLUTIONS: website