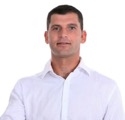 Kevin Hill |
Kevin Hill heads up the marketing efforts and provides technical expertise to the sales and service teams at Quality Scales Unlimited in Byron, California. He enjoys everything mechanical and electronic, computers, the internet and spending time with family.
TIn order to maximise productivity in your warehouse, you need to ensure each and every part, section, piece of equipment and human resource that you have in place is working as per its specifications.
Anything that might be causing downtime or delays must be attended to as soon as possible.
In a nutshell, any second your machines are down due to damage translates into revenue loss for your warehouse since little or no production is taking place. It also means your workers will have to work for extra hours to make up for any lost time and, consequently, you are going to have to dig deeper into your pockets to pay for the overtime hours.
The good thing, however, is that there is something you can do to avoid all that. Try these tips:
1. Service your machinery regularlyMake a point to establish a plan to regularly maintain your machinery without fail. This will save your machines from complete failure since you will have noted the problem early enough. Another advantage of regular maintenance is that your warehouse will continue its operations smoothly, without breakdown of machinery, improving on your efficiency. Servicing of machinery will, therefore, help detect any likely problems before they result in major time and money loss to your business.
The importance you attach to those occasions of installing new machines should be the same importance that you give to the maintenance of the old ones.
2. Work using up-to-date machineryIf your equipment is outdated, it's time to replace it. This is not only because old machines may be slowing down your manufacturing processes, but because they are also expensive to service. Their repair parts may take longer to find in the market if they are no longer manufactured, subjecting you to even more downtime.
Manufacturers are always working towards making improved models in terms of speed and productivity. Don't insist on working with slow machines when new technology presents you with the opportunity of improving your warehouse productivity.
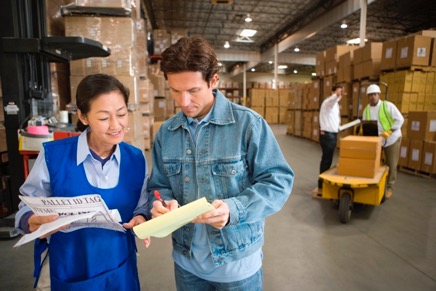 Increasing productivity through streamlining the process |
3. Keep an eye on all manufacturing processesJust like any other business, all existing departments are related and one cannot work in isolation. Likewise, in your warehouse, what happens in one process will definitely affect every other process in the production chain.
Being able to pinpoint what is causing delays early enough is critical in ensuring your business is performing at its best. This kind of evaluation also ensures that any items processed at the warehouse are delivered to clients promptly. A happy and satisfied customer is what keeps businesses going and growing as well.
4. Make use of truck scalesBy using
truck scales, you are already improving on your productivity. Forklift scales make lifting, weighing, moving and recording of loads possible in a single operation. They have electronic sensors which make the weighing of loads accurate. These scales have no springs or hydraulics fitted in them, hence their ability to withstand any jolts without interfering with their accuracy.
5. Monitor efficiency levelsSo you bought a new piece of equipment and you think you increased efficiency in your warehouse? This may be just a tip of the iceberg; you need to do much, much more.
Keeping track of your efficiency means you are well in line with all your operations. Your profit is a direct reflection of how efficient your operations are. Be proactive and analyse how efficient every process is in order to maximise on profits.
6. Create awareness about downtime among your employees If you have employees who understand their jobs well, you are saving on time loss. Refresher courses to train them on how the machines work will improve their efficiency.
Make your employees understand the effects of downtime for the business and involve them in suggestions as to how it can be limited.
7. Make the design and layout of your warehouse betterImproving the layout of your warehouse can be a simple yet very effective step towards increasing productivity and reducing downtime.
Many warehouses are designed to maximise space for pallets or racking. The problem with this kind of layout is that it severely hinders the flow of staff and products through the warehouse. Get help to turn around the layout of your warehouse to one that promotes efficiency.
8. Make processes easier, reduce touches and bring down costsRe-evaluate the physical steps and processes that are involved in order fulfillment and product flow and see whether there has been the layering of new functions over pre-existing ones. Productivity will be improved by making certain that you generally have fewer steps or procedures within your product flow, hence requiring fewer touches because that translates into lower production costs.
9. Think of automation and build a warehouse within a warehouseAutomating processes that require extensive travel time inside your warehouse will improve productivity to a great extent. Consider installing conveyance and multi-level towers to reduce the energy and time wasted by your order pickers moving products around.
Grouping even a quarter of your stock keeping units that accomplish around two-third of your orders will tremendously improve the efficiency of your pickers. Simply ensure that a ratio of 80-20 is designated to the zone for accommodating high-volume activities.