Pulp & Paper International magazine's latest statistics posted on the Finnish Forest Industries Federation website puts the global paper and paperboard production in 2003, at 339 million tons. Forkliftaction.com News reporter Christine Liew looks at the equipment used to handle logs, wood chips, pulp bales, sheeted paper and paper rolls, which are the raw materials and finished products, in this multi-billion dollar industry.A close partnershipForklifts are machines that lift and move a diverse range of materials. Combine them with attachments, and they perform tasks in very specific industries. In the paper industry, the forklift is fitted with different types of attachments to lift and carry materials along the industry's logistics line.
How does a forklift attachment manufacturer get its product to the end user? Forkliftaction.com News spoke to Uwe Killmann, marketing & sales director of Kaup Gmbh & Co KG, a German manufacturer of forklift attachments.
"The forklift distributor, who is the closest to the end user in clarifying relevant specifications [for attachments], plays an important role in co-operating with us to offer the materials handling solution of forklift and attachment to the customer, not the forklift manufacturer," Killmann said.
"In this sense, we and our international representative network are always working closely with forklift distributors. Some of our competitors work hard to influence end users directly and promote themselves in order to generate inquiries and orders.
"We respect our colleagues in the industry but we refrain from contacting end users in any type of industry without involving our forklift partners," he said.
Just as forklift attachments work when combined with forklifts, Kaup, as an attachment manufacturer, has close ties with forklift distributors.
Killmann said Kaup consulted its partners in the forklift industry for information on loads and handling tasks, which their partners obtain directly from end users.
"Forklift driver training is another important service carried out by forklift distributors. Roll clamps could pose a difficulty for forklift drivers," he said.
US-based forklift attachment manufacturer Cascade Corporation also worked closely with the forklift industry.
"Cascade sells its products to Lift truck OEM's and their authorised dealers," says Brad Vandehey, Cascade Corp's product manager. OEM attachement sales and installation benefit the dealer by providing a complete package installed at the OEM factory that is a turnkey sale providing an OEM-designed package with no unknown costs."
The four different end users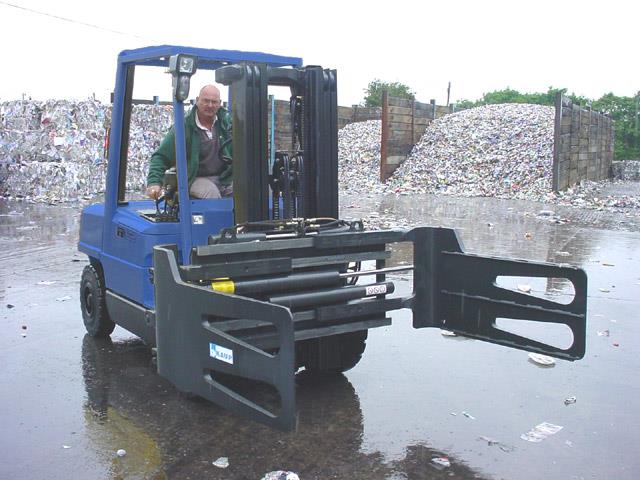 Kaup's general purpose bale clamp. |
According to Killmann, all end users may use general forklift attachments, like sideshifters, fork positioners, drum clamps and working platforms or crane jibs but there are also specific attachments for different end users.
"Pulp mills handle raw materials like logs or wood chips and their finished product is pulp bales. Rotators are used to handle containers of wood chips while pulp bale clamps handle pulp bales," he said.
"In paper mills, pulp bale clamps and recycling bale clamps handle pulp bales and recycling paper bales while fork positioners, pallet handlers, rotating roll clamps and non-rotating roll clamps handle the finished product like sheeted graphic paper on pallets or paper rolls.
"Roll clamps come in different sizes and have different sizes and shapes of pads. They are used to handle different types and grades of paper.
"As you can imagine, a tissue paper roll will be very different in volume, weight, diameter, width and density compared to a roll of newsprint," Killmann said.
The third end users were ports, harbours, paper wholesalers or "any type of logistics provider". They handle only finished products, either paper rolls or sheeted paper on pallets. Fork positioners, pallet handlers, telescopic forks, rotating roll clamps and non-rotating roll clamps were attached to forklifts to move the finished products. The fourth end users, converters and print shops, handle the same product and use the same forklift attachments.
Billion dollar damage each yearOf the 339 million tons of paper produced globally in 2003, Asia accounted for 32 per cent of production, North America 30 per cent, the European Union 26 per cent, and the remaining 12 per cent was from other parts of the world.
Vandehey estimates three to five per cent of paper production is lost as a result of paper damage in the global paper industry each year.
"[Let's say I] estimate a one per cent paper damage per year. Loss attached to damage based on the production of 340 million tons a year is 3.4 million tons of paper.
"Using a conservative estimate of USD500 a ton, an estimated USD1.7 billion in damage each year is reasonable," Vandehey said.
"This is a lot of damage but it becomes clearer when you look at the number of times a roll is handled. Assuming one uses a conservative figure and says each paper roll weighs 2.5 tons, then the number of paper rolls handled is 136 million each year. If one uses seven handling sequences per roll, this equates to 952 million roll handling sequences a year. There is ample opportunity for damage to occur," he said.
Killmann said the forklift driver needed skill and experience to handle paper rolls.
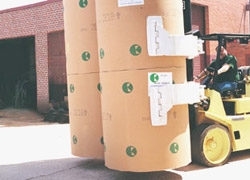 Cascade's 2-4 Roll Pivot Arm Clamp designed for multi-roll handling at mills and stevedores. |
"Due to the variation of diameters of different rolls, a high degree of skill and experience is necessary to grab the roll at the optimal point. Roll edge damage is a frequently cited issue and occurs when the driver has difficulties setting the exact vertical and lateral 90 degree position [of the paper clamp] to the paper roll," he said.
"Making the correct clamping pressure is difficult when roll weights and diameters vary a lot. Our clamps come with adjustable pressure regulation valves, which set one pressure for all rolls to be handled," Killmann said.
Cascade Corp spokesperson Madalyn Piarkatter agreed paper roll damage was a common problem for forklift drivers.
"Roll damage problems include torn layers and scuffing, out-of-roundness and core crushing, edge damage and roll dropping. We have developed options designed to control clamp force to accurately align the contact pads to the paper roll and securely lift and deposit rolls," she said.
One of Cascade's damage reduction options is adaptive force control (AFC), a computer-controlled clamping system. AFC monitors load weight as the roll is lifted and automatically adjusts the clamp force based on the weight. It then applies the optimum force needed to hold the load securely and eliminates the potential for damage from over clamping.
More rolls in one goOne of the ways to improve operator productivity is to use attachments that enable the handling of multiple paper rolls. Instead of using multiple forklifts and additional staff to move multiple paper rolls, a single forklift and forklift driver can move the paper rolls with a multi-roll clamp, Vandehey said.
"Mills and stevedores can have fairly long runs to move paper. Stevedores especially need to move paper quickly, such as when the ship is docked. Mills also have their peaks and valleys in production and multi-roll handling helps smooth out this issue," he said.
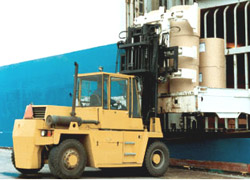 Cascade's 1- & 2-Stack Tower Clamp can handle two to eight paper rolls. |
Vandehey said Cascade's single and double wide-tower clamps were popular for this purpose. They can handle from two to eight rolls of newsprint, coated stock, kraft or linerboard. Risk of paper damage for multi-roll handling is not any greater than for single-roll handling. The driver has to exercise similar care and precision in the handling operations.
Improving technologyKaup claims its range of recycling bale clamps is the most highly developed in the world for handling baled recycled paper and general handling tasks in recycling plants and paper mills.
"A new bale clamp with a smooth, outer arm design has been introduced for easy entry between bale stacks without damage to neighbouring bales. Our standard sideshift system is independent of the clamping cylinders. The sideshift function is performed by specific sideshift cylinders," Killmann said.
"One advantage of this system is that we are able to fit a pressure regulation valve into the opening circuit of the arms. Opening of the arms usually happens with the piston head side, which means you have at least three times the force when operating a clamp compared to closing it.
"We have learned from monitoring our competitor's products that quite often bolts break or arms are damaged due to the typical opening and closing movement of the arms when drivers try to enter the bale stacks," he said.
Killmann said Kaup was adapting the technical specifications of its attachments to suit the increasing weight and size of paper rolls. At the end of 2004, Kaup delivered its largest ever rotating roll clamp to be operated on a 25 ton forklift at an Egyptian paper mill. The clamp can pick up rolls of tissue paper with a diameter of three metres and a weight of up to six tons.
Cascade's Piarkatter said Cascade was further developing products that provide automatic clamp force control.
"We are actively working on technology associated with automatic data capture and auto ID force control, which has a large potential as RFID and warehouse management systems develop and mature. We are developing products that will interface with these systems to provide benefits such as automatic clamp force control based on identifying what the product is," she said.