The explosion-proof forklift industry may be small but it is essential because it ensures forklifts do not spark disastrous workplace incidents. No organisation that counts the number of explosion-proof (EX) forklifts exists, but an industry source says the EX forklift market is around two per cent of the total forklift market. by
Christine LiewA range of usersForklifts that work in hazardous locations can be dangerous. The equipments' ignition sources, like sparking components such as motors, switches and controllers, and hot surfaces from motors, brakes and engine exhaust systems, when exposed to flammable gases, vapours, liquids and combustible powders and dusts, can cause fires or explosions.
The American Specialty Equipment website lists EX forklift users as industries involved in manufacturing, handling, processing or storing explosive or hazardous materials. Examples of materials are perfumes, cosmetics, paints, varnishes, printing ink, flour, confectionery, medicinal chemicals, botanical products, alkalies and chlorine, and synthetic rubber.
Other EX forklift users include facilities where combustible dusts are produced from handling materials like dried hay, starches and pastes, potatoes and grain. Locations where there are drying rooms for evaporating flammable solvents and spray or paint booths also require EX forklifts. So do sewage treatment facilities that create flammable gas byproducts and refrigerators that store volatile and flammable materials.
Warning: hazardous locationThe classifications of hazardous locations depend on the types of materials handled. There are two main ones.
In the USA, the division classification system consists of class 1 for flammable gases, vapours and liquids, further subdivided into divisions 1 & 2, groups B, C, D; class 2 for combustible dusts, subdivided into divisions 1 & 2, group G; and class 3 for ignitable fibres and flyings, subdivided into divisions 1 & 2. The National Electrical Code (NEC) establishes the requirements for electric forklifts used in the division classifications.
The other classification system is European- followed by many other countries - where workplaces are classified into zones. According to European directive ATEX 1999/92/EC, hazards associated with gases or vapours are classed either in zones 0, 1 or 2. Hazards associated with powders or dust particles are categorised as sones 20, 21 or 22.
Small but competitive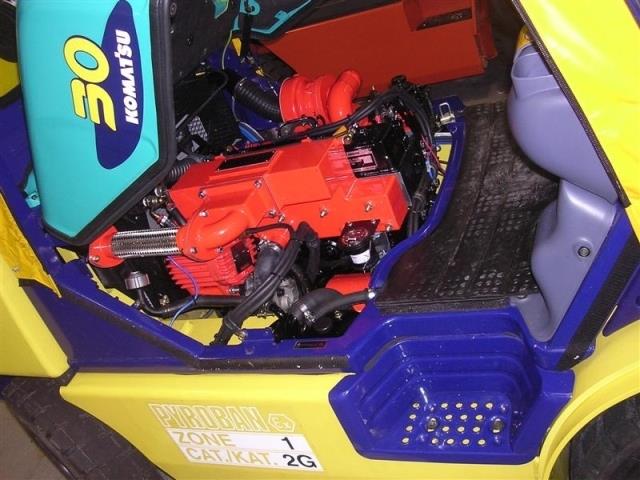 A standard forklift converted into an EX truck by Pyroban. |
EX forklifts are constructed from the ground up or converted from standard forklifts. Pyroban, a leading European EX systems provider, converts about 600 forklifts a year to a recognised EX standard. The company is the exclusive or an approved EX conversion supplier to forklift manufacturers like Toyota, Jungheinrich, Hyster and BT for conversions in accordance with European standards and directives.
Malcolm Davis, Pyroban's sales & marketing director in the UK, said it typically took four weeks to 12 weeks to convert a standard forklift to an EX truck.
"It depends on the size and specification of the truck. The process involves establishing the parameters of the truck you're converting, manufacturing materials, installing materials, testing the truck and benchmarking against the product and getting certification," he said.
Davis said there were at least two types of EX systems available.
"For storage and distribution areas where the hazard is not normally present, "active" systems that continually monitor the truck operator's working environment will provide audible and visual warning alarms if gases or vapour are detected. Before the atmosphere is explosive, the truck will automatically shutdown and a re-start will not be possible until the atmosphere is safe.
"For production and process areas where the hazard is likely to be present in normal operation, "passive" systems are employed. These use techniques such as EX housings for electric motors, intrinsically safe systems for control circuits and switches, and encapsulation and increased safety for components such as solenoids and batteries.
"With "active" and "passive" systems, tyres should be electrically conductive and forks clad in a spark-resistant material, such as brass or stainless steel. All systems need to be certified by appropriate authorities and supplied with detailed operating and maintenance handbooks," he said.
Robert Zuiderveld, US-based vice president of global marketing & sales for German-headquartered Sichelschmidt Global Sales, that manufactures EX forklifts, said the global market for EX forklifts was very competitive.
"People who convert can definitely do it much cheaper than those who build EX trucks from the ground up. We simply don't have the economy of scale that manufacturers such as Toyota, Nissan, Hyster or Crown have when building forklift trucks, however there are certain advantages of building from the ground up," he said.
"In the US, converted EX trucks are less popular due to certification concerns. In other cases the increase in the lead time to convert the truck becomes an issue. We have also received feedback from users who claim tracking down parts and documentation on conversion units can become a daunting task."
Zuiderveld said design appeared less important when it came to EX forklifts.
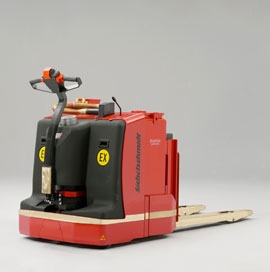 A Sichelschmidt EX pallet truck |
"In general, people who buy standard trucks are not the same people who buy EX trucks. In an EX application, functionality of equipment becomes more important than design and ergonomics, which are not regarded as necessities.
"One has to keep in mind that usage of EX trucks is minimal compared to conventional forklifts. In most EX applications, an EX truck will only be used for two to three hours in an eight-hour shift. If you compare this to the six to seven hours most standard trucks run in a non-hazardous environment, the shift of priorities can be easily justified," he said.
A truly international standardCurrently there are two main codes used by the industry to certify EX forklifts - the US NEC and the International Electrotechnical Commission (IEC), used by Europe and accepted worldwide.
A Pyroban brochure says the two codes have different EX protection philosophies. The NEC's philosophy is to contain explosions while the IEC's philosophy is to prevent and contain explosions. The NEC is not turned into laws while the IEC is.
Another main difference is enforcement of the codes. Zuiderveld said the NEC was enforced by the "local authority having jurisdiction". That could be the owner's own engineering judgement, insurance companies or a US federal, state or local agency such as OSHA and local fire marshals. The IEC is enforced by local governments.
Zuiderveld, who had been based in the US for eight years, said the IEC appeared to look out for the best interests of equipment users and public safety, while the US system (written by industry members through the National Fire Protection Association) seemed to favour the economic interests of EX equipment and component suppliers and the nationally recognised testing laboratories certifying equipment for use in the US.
Zuiderveld said the US system was "very confusing".
"The problem starts with the generalisation of division 1 explosion hazardous areas, which includes areas where explosive gases, dusts and fibres occur
all the time (IEC zone 0) or
most of the time (IEC zone 1) without clearly distinguishing one from another.
"Add to this the sheer volume of applicable codes and regulation, NEC, UL 1203, UL 1604, UL 583, NFPA 505, OSHA 1910.178 and ANSI, followed by the contradictions between them. For example, NEC in article 505 allows the use of internationally certified equipment based on the determination of the "local authority having jurisdiction", while the NFPA 505 "Fire Safety Standard for Powered Industrial Trucks" requires equipment to be NRTL (nationally recognised testing laboratory) certified.
"Another example is that EX forklifts must be tested and certified for Cclass 1, division 1 groups C&D in accordance with NEC, UL1203 and UL583, while NFPA 505 states that EX equipment can only be used in class 1, division 1 group C explosion hazardous areas. It is probably a good thing that the final responsibility for enforcement is as unclear as the codes and regulations themselves.
"It is not a surprise that multinational companies, like AKZO Nobel and Dupont, for example, use European certified equipment all over the world except for their US applications. US facilities are required to use US-certified equipment in an effort to limit their liability. By the same token, insurance companies will cover the IEC certified equipment in Europe applications, however they will not allow use of these trucks in similar US plants," Zuiderveld said.
"The international standard is based on the European standard (ATEX directives). The Americans are pushing to make the US standard a bigger part of the international standard. If you look at the US codes and regulations, they're outdated but the European one is more updated. The level of technology of explosion protection in the US is still at the same level as in Europe in the 1970s."
Zuiderveld said only clear acceptance of certification by internationally recognised testing laboratories in the US codes and regulations would open the US market to European certified equipment.
"NPFA members appear to be delaying integration of the IEC so they can catch up. Protection of the US market from foreign suppliers only offers short-term benefits, which will leave them behind on a global level in the long run. To be honest, if no changes are made to the current US code writing and enforcement system it will take another 10 to 20 years before we have a [truly] international standard."
An American company's perspective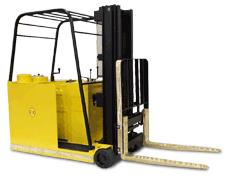 A Gregory EX truck. |
Forkliftaction.com News contacted American Specialty Equipment (ASE) to get the company's opinion on the US EX industry. The New Jersey-based company manufactures Gregory EX trucks. ASE and Landoll Corporation (Drexel forklifts) are the only two manufacturers of EX forklifts in the US.
Bob Doran, vice president of sales for ASE, said the EX market in the US experienced "slow and cautious growth".
"End users are evaluating their requirements in light of safety and expense considerations. EX equipment is usually a large investment of funds. We are continually creating an awareness of the importance of EX equipment with our customers and potential customers," Doran said.
(An industry source told
Forkliftaction.com News constructed EX forklifts cost three to four times more than standard forklifts while converted EX forklifts cost double the price of standard forklifts.)
He said for liability reasons American users preferred constructed EX forklifts to converted EX forklifts. "The truly constructed units follow the procedures set forth in UL583 (the Underwriters' Laboratories standard for electric forklifts) and are labelled by an NRTL. Tested and labelled EX forklifts are a lot safer than "built to standards conversion" forklifts without labels."
Doran said US standards were more stringent.
"While the European and US class I, zone systems share many similarities, according to our premier testing NRTL, UL, there are key differences that still exist, including wiring and sealing, grounding, markings and application of requirements that address the risk of fire and electrical shock associated with the trucks, in addition to the requirements that address the risk of explosion. The European units do not meet these standards unless modified to comply. Their battery design and cable exposure without proper protection is one such dramatic area."
Doran did not agree that the level of EX protection in the US was behind European counterparts. "The current European EX standards cannot meet US standards for division 1. American Specialty is the only UL labelled EX forklift manufacturer labelled for groups C, D and G for division 1. No other manufacturer can make that statement.
"That label is equivalent to European zones 0, 1 and 2. The current European units operating in the USA only have approvals on their pedestrian units and only for group D, division 1. They do not have approvals for groups C and G, division 1 because they cannot meet the requirements with their current equipment," he said.
On the question of whether the US EX industry would welcome the integration of US codes into the international code, Doran said: "There has been an effort for harmonisation for years on the codes. The US will not compromise on its standard procedures for testing and constructing EX equipment. Safety for the work force and work place are and will always be at the forefront for US EX forklifts.
EX forklift codes & regulations and certification:
www.iec.ch/index.html
www.ul.com/hazloc