Tens of thousands of workers are injured in forklift-related incidents in the US alone each year and about 100 of such incidents result in fatalities.
Christine Liew investigates the dangers in warehouses and some of the solutions.
Experts say tip-overs and blind spots for reversing forklifts are the two big safety concerns for those who work in warehouses.
Alicia Lemke is owner and senior consultant of Wisconsin, US-based Complete Safety Concepts (CSC), a materials handling safety specialist that has trained several thousand operators and trainers throughout the US. Before establishing CSC, Lemke worked for the largest Toyota forklift dealership in North America.
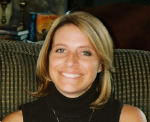 Alicia Lemke |
She says in her eight years' experience in occupational health and safety, most forklift incidents cause injuries to the pedestrians working around forklifts but it is tip-overs that cause the most fatalities among operators.
Dave Hoover of Forklift Training Systems, Ohio, US agrees tip-overs kill more workers than any other accident type. This is exacerbated by most forklift operators' reluctance to wear seatbelts.
Hoover, also
Forkliftaction.com News's Safety First columnist, said in our
end-of-year review that even the bright orange-coloured belts with electronic cut-outs are ineffective. Operators easily defeat their purpose by buckling and sitting on them.
"Putting a guard over the operator like on a rollercoaster would not be well accepted, at least here in the US. So what about a 'smart belt' that won't let the forklift operate unless the operator is buckled?"
Lemke says operators are constantly "on and off" forklifts and so they refuse to strap on the safety device.
"I believe that they will not wear them until it's aggressively enforced. Every manager, supervisor, foreman, safety person and trainer has the responsibility of enforcing forklift safety."
Safety belt substituteWhile not exactly a rollercoaster-like guard or 'smart belt', a Dutch company boasts its seatbelt substitute can save lives.
Peter Brusse from forklift importer Crepa BV of Rijswijk, Netherlands says the Pilot Protector is a very good replacement for the safety belt and more acceptable to operators. Crepa, which employs 230 workers and had a turnover of EUR55 million (USD83 million) in 2007, also imports and sells forklift safety products in the Benelux.
Brusse says that the safety belt is a cheap solution for the employer but uncomfortable for operators. "Safety belts press into the operator's stomach.
"With the Pilot Protector, you are always protected and the driver has more freedom of movement and faster step-in, step-out time".
Consisting of two "door handles", the device, manufactured by a company in Kamp-Lintfort, Germany, prevents the operator from falling out of the cabin.
Brusse explains that the tested door system also prevents the operator from jumping off the forklift when it suddenly falls over and decreases his/her risk of being hit by the forklift's protective roof.
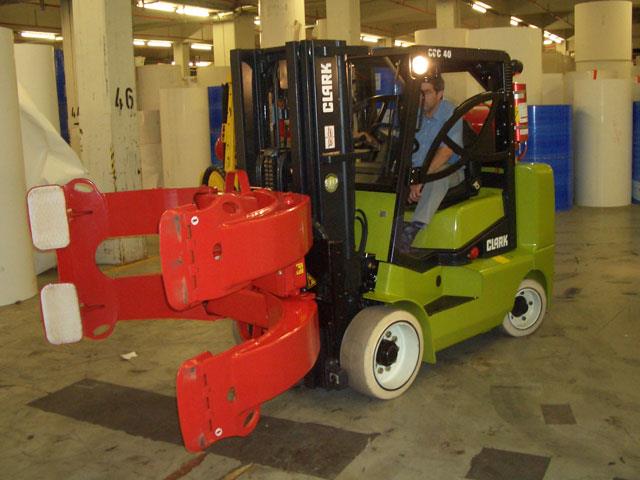 Stora Enso's Clark forklift equipped with Pilot Protector |
One of the Pilot Protector's customers is Swedish-Finnish company Stora Enso's Baienfurt site near Ravensburg, Germany. Stora Enso delivers up to 210,000 tons of cardboard to the packaging industry, printing plants, publishers and wholesalers in Germany.
Hald & Grunewald, a Clark dealer from Herrenberg, Germany, supplied the company with a CGC 40 Clark LPG forklift equipped with an Auramo paper roll clamp and the Pilot Protector.
Ingo Rose from Clark Material Handling Europe says the Pilot Protector was installed to hold the driver back in the operator compartment "in every situation", leaving Stora Enso deeply impressed.
In addition to the driver restraint system, the Clark forklift was equipped with a camera system, reversing sensors and a fire extinguisher system.
Curve ControlJungheinrich forklift users can choose the Curve Control technology option to reduce the risk of tip-overs. The Curve Control system automatically and gradually reduces the forklift's maximum speed according to its turning angle.
Greg Mason, Jungheinrich Lift Truck Corp's general manager for products and training in Richmond, Virginia, US, says the system uses computer algorithms to accurately determine the best combination of speed and turning angle for optimum levels of safety and productivity.
"The technology aims to reduce the risk of the forklift tipping over due to the operator turning the steering wheel when travelling too fast."
The extent to which the forklift's maximum speed is decreased is directly related to its turning angle. For example, a five degree turn represents no tip-over risk and so maximum speed is not reduced. But if the operator makes a 90 degree angle turn, the forklift's maximum speed is automatically limited as a tip-over risk is greater when turning at higher speeds.
Pedestrian SafetyThrough a speed limiting device and a driver restraint system, forklift operators can be protected. But what about the pedestrian who is working outside and not in a forklift compartment?
Lemke says warehouses are not really designed for pedestrian access.
"Visibility in warehouses and racking systems is extremely limited, yet most companies don't restrict or enforce policies to restrict pedestrian traffic through these blind areas, which can lead to accidents between forklifts and pedestrians."
She says companies can prevent pedestrian injury by conducting pedestrian awareness training, enforce rules on forklift operators and pedestrians, provide alternative access routes for pedestrians and caution workers by showing photos of forklift incidents.
White sound alarmForklift safety product companies supply a variety of devices to prevent accidents between forklifts and pedestrians, particularly when forklifts are reversing.
Brigade Electronics Plc of Kent, UK claims it is the only company in the world to provide a complete range of reversing safety systems. One of its products is the bbs-tek reversing alarm that has been written into the Olympic Delivery Authority's Code of Construction Practice for the 2012 Olympic Games and all construction sites in the greater London area.
Brigade general manager Henry Morgan boasts there are over 8,000 bbs-tek alarms fitted in US cities, ports and construction sites. He says the alarm is the only reverse alarm to be approved by New York City's Department of Environment Protection for use near "sensitive areas" like schools, hospitals and places of worship.
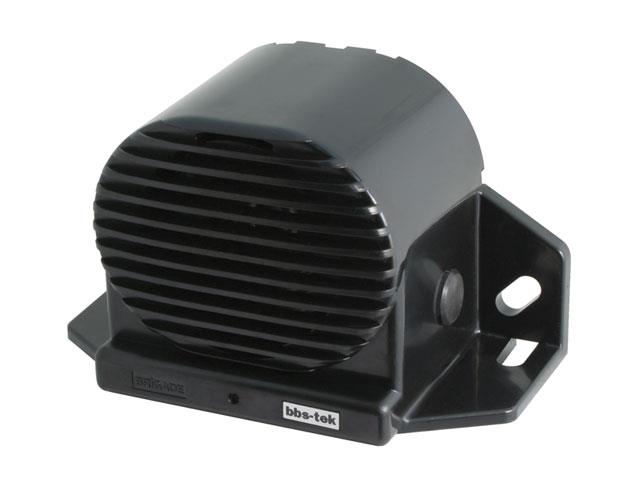 Brigade Electronics' broadband based sound alarm |
With sound levels ranging from 77dB(A) to 97dB(A), the alarm has a small microphone that measures the ambient sound pressure level and then adjusts the alarm to maintain a 5dB-10dB higher volume so it can be heard. Besides forklifts, it is used for trucks, buses and light mobile plant machinery.
Lemke says reverse alarms are only useful if the pedestrian can be alerted to the hazard.
"Unfortunately, because of the monotone, regularly intervaled alarm noise becomes part of the background noise and people except the forklift operator don't actively hear it."
Morgan says the bbs-tek alarm uses broadband sound commonly known as "white sound" that is more effective than conventional alarms. The alarm is the only broadband sound alarm available as Brigade holds the patent to using broadband sound for reversing alarms.
"The sound is directional, unlike tonal alarms, enabling people to detect which vehicle is reversing and taking appropriate action to move to safety."
Health and Safety Executive statistics show that being hit by a moving vehicle was the third most common cause of accidents involving workplace transport in 2006/07.
The HSE recorded a 17% decrease in accidents caused by reversing vehicles in the workplace in the last two years.
"The decrease is encouraging but by fitting reversing alarms and reversing cameras, the figure would be significantly lower," Morgan says.
Serious injuriesKristopher Seluga is a consultant with forensic engineering firm Technology Associates of Stamford, Connecticut, US that investigates a variety of accidents including forklift accidents. Seluga and his colleagues have been hired by plaintiff and defendant attorneys to investigate forklift incidents resulting in personal injuries, and have testified as expert witnesses in court.
In his role as a forensic consultant, most forklift incidents he has investigated involve the driver rather than pedestrians. (Seluga does not investigate incidents related to the negligence of the injured party's employer as those incidents are covered under worker's compensation laws and the employee is prevented from suing his or her employer.)
"From the statistics I have seen, the most common type of accident is a forklift striking a fixed object and injuring the operator," he notes.
One of the worst cases Seluga has been involved in centred on a driver who had a severely fractured leg caused by a stand-up forklift colliding a metal railing that entered the operator compartment and hit the operator. The case went to trial and the operator was awarded about USD3.5 million from the forklift manufacturer because the forklift was not built with a door to protect the driver.
"Better operator protection structures as standard features would go a long way towards preventing many injuries."
Preventing whiplash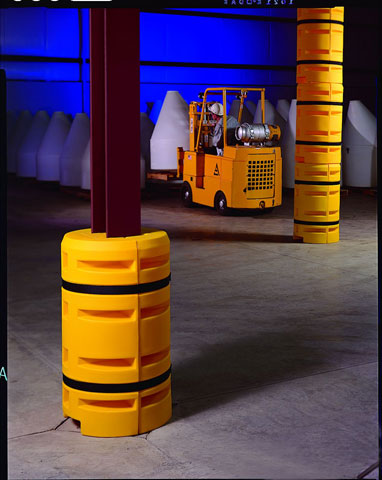 The Column Sentry protects racks from forklift impacts |
Lemke says racking supports seem to continually get struck by forklifts and loads.
"This damages the structural stability and causes racks to fail and loads to fall. Careful driving and replacement of damaged rack supports (are) critical."
This need has created a niche for manufacturers like Column Sentry Protection Products of Lakewood, Ohio, US. The firm has sold over 70,000 of its Column Sentry products worldwide to clients including General Motors, Dana Corp and Chrysler Corp.
The Column Sentry, a protective shell for steel columns, consists of two low-density polyethylene symmetrical halves that are strapped around structural columns, forming a protective cylinder. They are semi-flexible and stress crack-resistant. Each half is an airtight shell designed with air-chambers to absorb nearly 90% of the energy produced when a forklift accidentally collides with a warehouse's steel columns.
Weighing about 34kg (75lbs) and 64cm (25 inches) in diameter, the protective shell lessens damage on columns and racks, and prevents the bending of building structures and rack collapse when a forklift crashes. By absorbing energy from the impact, it also prevents whiplash for the operator.
VNA operationA number of solutions are available for very narrow aisle (VNA) applications. These include:
RFIDThe use of advanced technology for forklift safety in warehouses is evident in Jungheinrich turret trucks. RFID technology has been incorporated into the control of the EKX513 and EKX515 turret trucks to help them avoid hitting warehouse obstructions.
RFID transponders are located in the warehouse floor and RFID transponder readers are mounted on the turret truck. When the truck is installed in the warehouse, the transponders are programmed with information that identifies the precise location of the transponder and corresponding truck operational restriction information.
For example, in an area of an aisle that has a low-hanging obstruction, transponders and truck controls can automatically limit the lift height of the truck in that specific area to prevent an inattentive operator from driving into the obstruction.
PSSPersonnel safety system (PSS) is also available on the EKX 515 series turret truck. The PSS uses a laser scanner to monitor any obstructions that may exist either in front of (or behind when travelling in reverse) the turret truck operating in a very narrow aisle.
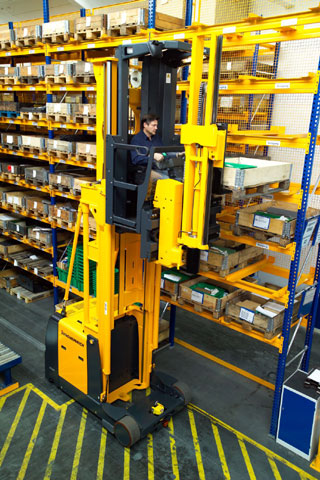 Jungheinrich EKX turret truck |
VNA operation is unique because there is very little room between the truck and racking. So if someone is in the aisle at the same time as the forklift, there is no place for that person to go to get out of the forklift's way.
The PSS scanner is intended to protect against the forklift hitting the pedestrian by first slowing the truck down automatically and then stopping the truck automatically if the truck gets too close to the pedestrian or any object that is in the forklift's path.
The scanner can be set to scan any prescribed distance in front of the truck.
"Ideally, this is set far enough out so the speed of the truck can be reduced to a stop prior to the truck coming into contact with the obstruction in the aisle," says Jungheinrich's Mason. "In theory, it could prevent a head-on collision between two trucks provided the scanning distance was set far enough so the system would have the time to cause both trucks to be seen and then slow down and stop prior to a collision." Under normal circumstances, however, users do not have more than one VNA truck operating in a VNA at any given time.
The system works by the PSS sending a signal to the truck controller identifying that there is an obstruction in the truck's travel path. The controller then automatically starts to reduce the truck's speed. If the obstruction remains in the truck's path and starts to get closer, the PSS sends a signal to the controller indicating that the truck should be stopped.
The scanner can scan for loads and pallets at the first level of racking and even small boxes sticking out into the aisle. It is mounted on the truck chassis, low to the ground and is intended to scan the aisle, reducing the potential for product or forklift damage.
- Because warehouses are designed more to meet the needs of those determined to maximise the use of storage space than the needs of forklift operators and pedestrians, safety will remain a vital issue. Forkliftaction.com News will continue to highlight the need for safety measures through articles like the recent Safety First column on Pedestrian Safety and this week's on Dock Safety.