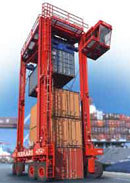 CVS Ferrari's straddle carriers have electrical steering control. |
Noell and Kalmar are strong players in the straddle carrier market but newcomers and smaller companies including CVS Ferrari, Trevolution and Isoloader have entered the market with unique and cost-effective machines.
Christine Liew reports.
CVS Ferrari SpA is one of the better-known newcomers in the straddle carrier market. Like any materials handling manufacturer breaking into a market significantly dominated by giants, CVS knows its machines have to be unique.
The Italian company recently delivered four 40 ton diesel-hydrostatic units, with one-over-three capability, to Port Lattakia in Syria.
"As a newcomer, CVS has had to bring innovations in order to break (into) the market," says sales director Paolo Groppi. He estimates the straddle carrier market size to be between 400 and 450 units a year.
CVS claims to manufacture the world's only straddle carrier that can lift one-over-two or one-over-three, fully hydrostatically, with motors fitted inside the machine's wheel hubs. The hydrostatic drive cuts maintenance costs because there are no mechanical parts involved in the transfer of torque from the engine to the wheels that could break down.
The machine's closed circuit made of variable displacement pumps and motors has a lifespan of over 24,000 hours. CVS estimates it is 5%-8% more fuel efficient than its competitors.
"Our strategy has been to develop a machine with much higher technological content than the one available from the leaders," Groppi says. "We focused on providing a machine with higher efficiency in terms of fuel consumption and lower energy demand."
Another fuel-saving option is CVS's diesel-electric straddle carrier that follows the same concept of the hydrostatic straddle carrier. Electrical motors are fitted inside the wheel hubs and the straddle carrier uses permanent magnet motors for generating energy. The motor allows energy to be transferred back into the engine and recovered in a hydraulic cylinder.
"If you calculate the carbon dioxide emissions that you save by the lower fuel consumption, you have a really fantastic impact on our planet," Groppi says. He explains that the diesel electric is 10%-15% more fuel efficient than its competitors.
"Not happy with this result, we are now installing on the diesel-electric a newly patented 'energy regenerating system' able to store inside the hydraulic cylinders the energy generated by the electric motors when the brakes are used or when the winch is lowering a laden container," he adds.
With this system, energy is supplied back to the system and fuel consumption is reduced by a further 10%.
Groppi says the hydrostatic drive straddle carrier costs about 15% less than the diesel-electric but the latter is more economical in the long term as it consumes less fuel.
CVS recently delivered five 50 ton twin-lift, diesel-electric straddle carriers with one-over-two capability to HHLA's container terminal in Burchardkai CTB in the German port of Hamburg, with options for an additional five units.
The lower noise level of the diesel-electric machines is becoming an important consideration for terminals, especially those located near residential areas. Groppi says diesel-electric straddle carriers can be about 4dB quieter than other straddle carriers, when noise is measured at 20 metres from the machine.
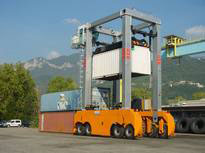 Trevolution's long experience in the design and production of lifting and transportation equipment was the decisive factor in the creation of the LCS-SC straddle carrier. |
Another Italian company new to the market is Trevolution SpA. Headquartered in Lecco, about 40km north of Milan, with offices near Verona and branches in China, Turkey and theUSA, Trevolution has made mobile cranes under the CMR brand since 1966. It specialises in manufacturing large-sized and high-performance rubber-tyred gantry cranes.
Today, it produces the 20-1,000 ton LCS Series for handling and moving containers in terminals and for intermodal operations, for towing vessels in marinas and shipyards, and handling and moving prefabricated concrete items and other materials in yards.
In October 2007, it announced the successful testing of its first straddle carrier. This followed one year of development in collaboration with African National Engineering Port Maintenance of Durban, South Africa.
Trevolution says ease of use and maintenance are the straddle carrier's best features.
"The only valid alternative to global market leaders", safety, reliability, low-running costs and short work cycle times are the straddle carrier's main features, Trevolution adds.
The eight-wheeled, 40 ton LCS-SC straddle carrier has one-over-two and one-over-three capabilities and comes with a telescopic spreader. Trevolution expects to install 10 units this year.
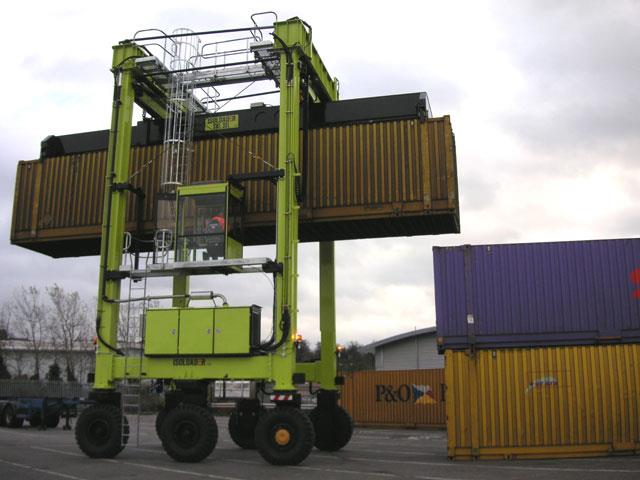 "Our straddles are lighter and much more manoeuvrable than standard port straddle carriers," says Eric Ronco. |
Australian company Isoloader makes straddle carriers for intermodal operations, rather than major port terminals. As such, it competes mainly with manufacturers of forklifts and reach stackers.
"Our straddles are lighter and much more manoeuvrable than standard port straddle carriers," says business development manager Eric Ronco.
Ronco agrees there is little room for newcomers in main port terminals, but "plenty in other operations".
"We are bringing to the market an effective cost and logistics alternative to conventional container handling machines people are used to. On the logistics front, Ronco says Isoloader's straddle carriers offer 50% more stacking density for order picking compared to competitors.
Originally manufacturing to fill a need in the Australian market, the company now has business overseas.
"Last year was a good year for us and 2008 will definitely be better with our development in Europe linked to the development of rail terminals all over Europe," Ronco says.
The Isoloader range of straddle carriers has been developed over the past 30 years, responding to the growing local needs.
"The first Isoloader straddle was developed for the handling of aluminium ingots for a smelter in Australia. Then we developed a solution for handling very few containers a day, the LiftingFrame, then to carry the container around as well, the EconoLifter. Then the customer needed to stack to save space (the Container Handler) and when the customers needed to stack even more and travel fast, the Transporter was born," Ronco says, summarising the company's straddle carrier history.
He names "capital price, running cost and maintenance costs" as Isoloader straddle carriers' edge over competitors and explains that the machines are only competitive to handle full containers.
A LiftingFrame costs AUD65,000 (USD62,504), about 15% of the of a 35-tonne reach stacker. The top-of-the-range three-high Transporter is 10% costlier than an equivalent reach stacker.
"In any case, even with our Transporter, large savings are obtained when considering maintenance and operating costs, which would be at least 30% less," Ronco says. This does not include pavement maintenance as the wheel loading of Isoloader straddle carriers is 15 tonnes maximum, compared to a reach stacker's 60-80 tonnes.
While the straddle carriers are more cost-effective, forklifts and reach stackers are specifically adapted for block stacking operation, typically for loading ships or handling empty container handlers as little or no order picking is required. Straddle carriers are more effective for order picking, Ronco says.
Isoloader is currently working on autosteering, using camera vision. It is also doing its part to improve its green credentials by making its machines more fuel-efficient through energy regeneration when loads are lowered.
The giants in the marketAs container traffic grows and ports worldwide boost capacity, Kalmar Industries and Noell Mobile Systems GmbH have received the bulk of the world's straddle carrier orders. Below are just some of the orders that the companies have publicised.
2008- Transnet Port Terminals of South Africa ordered 30 Kalmar CSC440 straddle carriers for its operations at Durban Container Terminal in the Port of Durban. Delivery complete by January 2009.
- Eurogate has ordered 48 Kalmar ESC 440 W straddle carriers for its operations in Germany. Eurogate Container Terminal Bremerhaven will receive 22 units, Eurogate Container Terminal Hamburg, 13 units, and another 13 for MSC Gate Bremerhaven terminal.
- Finnish port operator Steveco Oy ordered 10 Kalmar ESC440W straddle carriers for the Mussalo Container Terminal in the Port of Kotka. Delivery complete by October 2009.
- Port of Tacoma ordered 7 Kalmar CSC 350 straddler carriers for on-dock intermodal rail operations. The new order adds to its existing fleet of 26 Kalmar straddle carriers. Kalmar has been supplying straddle carriers to the Port of Tacoma since 1986.
- VPA Virginia Port Authority ordered 33 diesel-electric NSC 634 E units in February 2007, the biggest single contract for Noell.
2007- Medcenter Container Terminal SpA ordered 30 Kalmar CSC 440 and CSC 340 straddle carriers for its Gioia Taurao facility in Italy. The company also operates 23 Kalmar straddle carriers at its Fisherman Islands automated straddle carrier terminal in Brisbane, the first terminal of its kind in the world.
- Patrick Corp ordered 15 Kalmar CSC 350 and ESC 350 straddle carriers for container terminals in Melbourne and Sydney.
- TCB Container Terminal Barcelona ordered 12 diesel-electric Noell straddle carriers for the first time.
- MSC Gate Bremerhaven GmbH & Co KG and North Sea Terminal Bremerhaven (NTB) GmbH & Co ordered 17 Kalmar ESC 440 W straddle carriers.
- HHLA's Container Terminal Burchardkai GmbH, at the Port of Hamburg, ordered 10 Kalmar ESC350 W units.
- DP World Adelaide ordered four new-generation Noell units for the Port of Adelaide in 2007.
- Port of Gothenburg and Medcenter Container Terminal SpA in Gioia Taurao, Italy ordered over 10 Noell straddle carriers each.