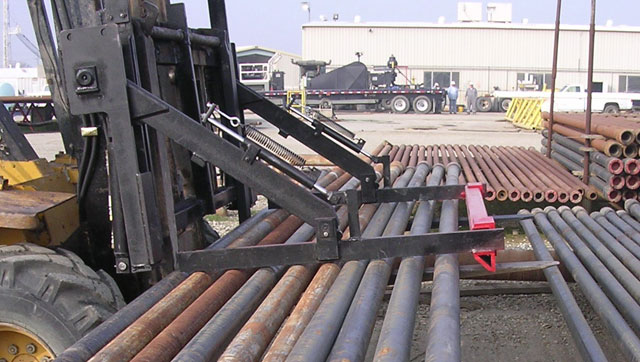 ULHS designed a pipe and pole hold-down clamp for a major US drilling company. |
Forklift clamps have made a difference in the safe and efficient operations of many companies worldwide.
Christine Liew looks at some of the latest forklift clamp innovations from Unit Load Handling Systems, Bolzoni-Auramo, Clark Equipment Australia and Cascade Corp.
Pipe and pole hold-down clampsUnit Load Handling Systems (ULHS) Inc of Friendswood, Texas was asked by a US drilling company operating in over 30 locations to help them improve safety and efficiency when handling 40-foot (12.2-metre) joints of drilling pipe.
"[They wanted to] minimise the effects of weight and thickness of the pipe clamps installed on existing forklifts for maximised forklift capacity retention," says ULHS president Brian Scally.
The customer was also keen to ensure the forklifts can still be used to handle standard-shaped cargo, have good operator visibility and that the clamping of the pipe against the fork blades would be safe and secure. The clamps would handle pipes 3.5- 24 inches (8.9-61.0cm) in diameter.
ULHS was also told that they could not replace the forklift masts or carriages when installing the clamp.
"No pinch points, no tools required to change from pipe to regular load handling. Use the forklifts as they were then configured," Scally explains.
ULHS came up with the WPH pipe and pole hold-down clamp to handle wide loads such as long pipe and pole products in yards and over rough terrain.
Before, the drilling company would pick up long and heavy drill pipes with the forks of a forklift. The pipes would be carried very slowly across rough gravel and dirt as there was no clamp device to hold the pipe against the forks. The WPH hold-down clamp prevents the pipe from bouncing, sliding and rolling, even when the forklift brakes or travels downhill.
Scally says the clamp is designed to connect to the space behind the forklift's carriage so that the attachment's weight is borne behind the fork face.
"[Hence] there is no loss of usable load dimension due to a clamp being face-mounted to the carriage," he says.
He adds that a pipe hold-down clamp would normally not be effective when mounted on this location. "A very clever aspect of this clamp is that we are able to effectively apply clamping force against both the pipe and the forks due to the design of our arms." ULHS has filed a patent application covering this aspect of the clamp's design.
The WPH clamp can lift vertically to 90 degrees and so clears the clamp out of the load bearing area of the forks, allowing the forklift to be used for other loads like pallets, machinery or spool. It will be fitted or retrofitted to forklifts using up to 72-inch (1,830 mm) forks. Most of the clamps that have been sold in the US, Mexico and Middle East have been retrofitted to forklifts.
Keeping paper rolls in shape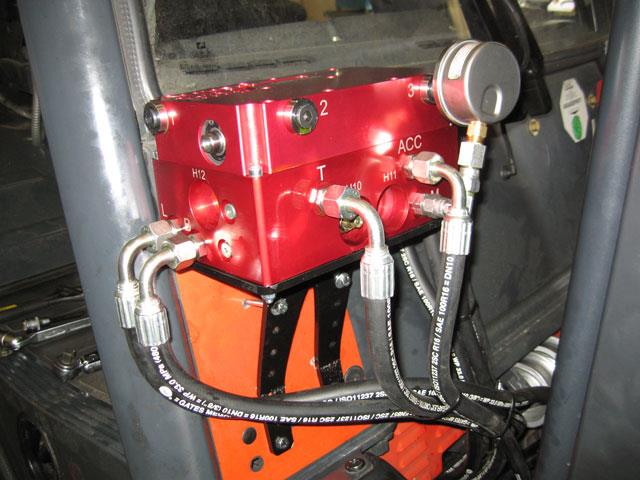 Force-Matic installed on a Linde H-35-393 forklift with Bolzoni-Auramo AR-30RJ-13 paper roll clamp. |
Leading Italian attachments specialist Bolzoni-Auramo SpA has been manufacturing forklift attachments for pulp bale and paper handling for over 60 years. Its product line includes over 300 different pulp- and paper-handling clamps.
Bolzoni's latest innovation for its paper roll clamps is the Force-Matic, a mechanical pressure control system that prevents overclamping.
Bolzoni sales & marketing director Carlo Fallarini says the new product fills a gap between different solutions available on the market.
Using the Force-Matic, each paper roll's weight is calculated hydraulically and the clamping force calculated according to pre-set parameters.
The system can sense the load's weight from two different sources, the lifting and tilting cylinders, and calculate the best clamping pressure. The valve works as a mechanical calculator, continuously adjusting the clamping pressure measured in the lifting and tilting cylinders. No electrical connections are required. The valve's heavy-duty aluminium construction combined with standard hydraulic components decrease the need for maintenance.
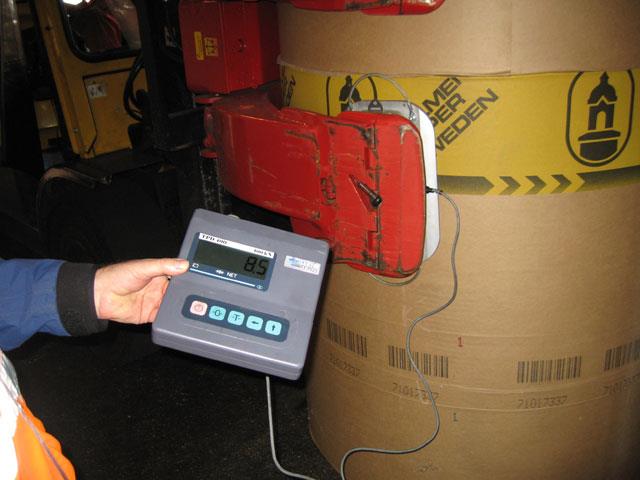 After installing the Force-Matic on the Linde forklift, Bolzoni-Auramo checked hydraulic pressure and tested clamping force. |
Fallarini says the Force-Matic valve fits 90% of Bolzini's paper roll clamps. The company only guarantees its function with its own clamps.
"We have already got feedback from customers using Force-Matic in their daily operation," says Lars Petersson, Bolzoni's forest products handling division manager.
He says customers are happy with the device's easy installation.
"We used approximately seven hours to convert the standard forklift and roll clamp to an efficient combination able to adjust clamping force to optimal value according to handled paper rolls". Previous systems require two to four days for installation.
The Canadian-made product that was launched at CeMAT 2008 in Hannover has been ordered by customers in Europe, US and Canada but Fallarini says it is too early to disclose who they are.
Tyre handling clamp for large forklifts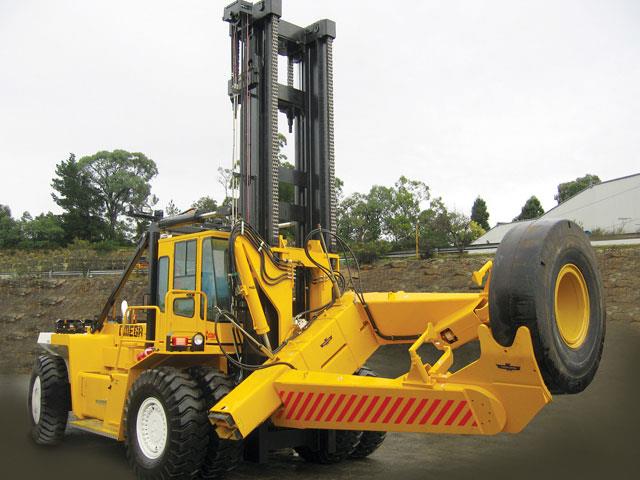 Clark Equipment Australia Pty Ltd produced a tyre handling clamp for BMA Blackwater Mine. |
Clark Equipment Australia Pty Ltd's heavy equipment division at Hornsby, New South Wales helped boost workplace safety for BMA Blackwater Mine with the delivery of two purpose-built Omega tyre handlers.
BMA maintenance staff worked closely with Clark to develop the clamp attachments that assist in changing huge earthmoving equipment tyres weighing up to 10 tonnes and meet the mining company's stringent safety and operational requirements.
Dave Little, BMA's tyre bay supervisor, says good visibility is critical for safe tyre handling operations and the new tyre handler's design gives the operator excellent visibility from the cab through an extra wide mast.
"These innovative tyre handlers play an important role in ensuring the safe and effective handling of heavy earthmoving tyres in and around the tyre bay, workshop and the tyre press facility," he adds.
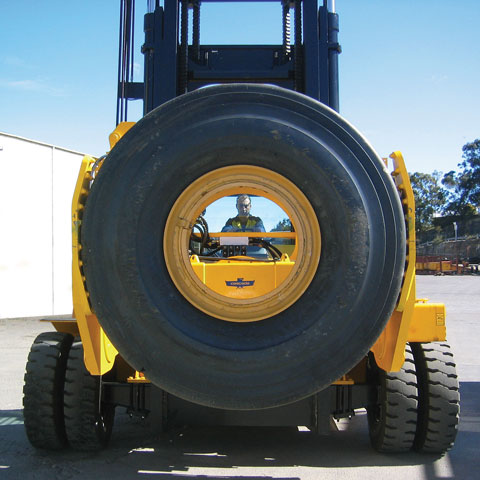 Good operator visibility is essential for tyre handling operations. |
The forklift operator is also guided by the tyre fitter, cameras and positive communications. Video cameras at the forklift's front and rear boost safety for the operator and tyre fitter while motion beepers augmented by strobe lights alert bystanders to the forklift's movements during a tyre change. Additionally, a two-way radio system with a dedicated channel for tyre fitting enables direct and uninterrupted communication between the operator and the tyre fitter
Little and his colleagues worked with Clark Equipment to develop training packages for the tyre handlers that were mapped into Blackwater's Black Coal Competencies tyre fitting package to provide a standard training process for each forklift supported by Clark Equipment.
The tyre handlers, designed and built in Australia by Clark Equipment Australia Pty Ltd, can be specified to suit specific mining and quarrying applications and are supported by a national service and parts network. After their launch over two years ago, purpose-built Omega tyre handlers are currently working on several mining sites across Australia.
Cascade's lumber-handling clampCascade Corp of Oregon, US custom-designed its 70D Turnaload clamp for Distribution Services & Warehousing Inc (DSWI) of Portland, Oregon. Founded by Ed Nukala in 1989, DSWI handles, stores and distributes paper, food, wood products and other goods.
DSWI was repeatedly running into problems unloading one of its regular shipments, rough wood plank bundles. The 16-foot (4.9-metre) bundles come tightly packed lengthwise in standard 40-foot cargo containers. DSWI staff struggled to pull the long, heavy loads out of the containers, often resorting to looping a chain around each bundle, and dragging it out with the forklift. The process was hazardous, time-consuming and inefficient.
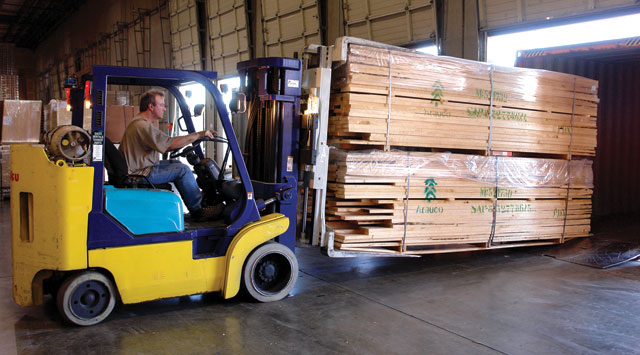 Forklift operators appreciate Cascade Corp's lumber-handling clamp. |
Working with Nukala and operations manager Randy Fitzhugh, Cascade designed a big clamp that opens to eight feet, securely grasps a lumber bundle and pulls it cleanly out of the container.
"It has really made a difference for us in time and maintenance cost. Hauling those bundles out by chain was slow and hard on the equipment," Nukala says.
"It has been a lifesaver," forklift operator Tom Young agrees. "Even if the bands break, the pressure of the forks above and below keeps the bundle together. We don't have to restack broken bundles by hand like we used to and there's less damage."
DSWI receives up to 20 containers a day. The lumber bundles are forwarded by flatbed semi truck to window and door manufacturers throughout the Northwest of the US.
"We handle a tremendous volume," Nukala says. "Our customers demand that we keep it moving out as fast as it moves in. That Cascade attachment has really made a difference in the time it takes to unload lumber."