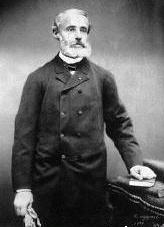 Gaston Planté |
Despite these times of technological advancements and alternative fuel sources, tried and true products like lead acid batteries stand the test of time. As
Annette Densham reports, people know they work and trust them to do the job required.
French physicist, Gaston Planté, invented the lead acid battery in 1859 and they have not changed much over the years. While their operational capacity has improved and the technology to charge and maintain batteries has been enhanced, they essentially do the same job - providing power - as they did 149 years ago.
However, it is the improvements such as fast charging, rejuvenation and low maintenance that cements this energy source's continued use by forklift operators and manufacturers.
It is easy to be distracted by the hype around emergent fuel sources, which may be cheaper and more environmentally friendly, but lead acid batteries will remain a stalwart power source in the materials handling world for at least the next 10 years.
David Bowen, product and sales manager of Linde UK, says lead acid batteries are here to stay.
"The majority of forklifts Linde supplies in the UK come with battery and charger and the majority of these batteries are lead acid batteries."
While there have been no major developments in the past decade, Richard Fitzgerald, from Granite Industrial Trucks Inc in the US, notes that "batteries that require less watering represent a slight improvement and the only major improvements are the quick charge systems".
He points out that while there may have been improvements in the quality of batteries, "any increase in performance is due to upgrades to forklift technology, not battery technology".
John Lawton, director of marketing at EnerSys, says the market is always looking for ways to squeeze additional performance from lead acid batteries while trying to reduce operating costs through lower maintenance requirements and more efficient battery charging.
"Lead acid batteries will remain the preferred option for the materials handing industry. It is a mature technology with world-wide availability and service infrastructure," he explains. "Lead acid batteries offer, by far, the lowest acquisition cost per KWh today for powering electric trucks."
One of the major areas of improvement in recent times has been battery charging and rejuvenation. Manufacturers and battery charging suppliers continue to make improvements to the battery's productivity, life span, efficiency, maintenance and recharging capacity.
Fiona Inglis, Australian national marketing manager of Century Batteries, believes fast charging is the most signification innovation of the last few years.
"Fast charging technology will revolutionise materials handling for companies that currently rely on battery changing to keep their companies running," she says.
Fast charging powers a battery on average four times faster than conventional or "slow chargers". It recharges batteries at high charge rates at opportune times during a work shift, like when an operator takes a break or changes shifts.
Century Yuasa Batteries recently partnered with AeroVironment to introduce PosiCharge to the Australian market. PosiCharge delivers a fast powerful charge during shift change and breaks. Ample power is returned, keeping the forklift running through multiple shifts and eliminating the need to change the battery. Another key feature of this charger is that it is universal and can charge any battery, regardless of size, make or model.
Inglis says fast charging means companies can maximise run time, eliminate battery changing, reduce operating costs and enhance productivity. This translates into cost savings as well as ease of charging, repairing and handling.
Rory Harvey-Kelly, general manger of sales for Komatsu Forklift in Europe, says battery technology has improved in terms of efficiency and user-friendliness.
"You no longer have to replace the whole battery plate when it breaks, thanks to the separation of the plates inside the battery. There is now the option to refill batteries. Being able to use a central filling system to distribute the liquid among all the opening mouths means batteries can be maintained easier and faster."
Lawton says EnerSys has responded to the need for easier maintenance with the introduction of the Hawker Water Less range - a low-maintenance flooded battery with extended topping-up intervals of four, eight or 13 weeks, depending on options and the charging technology used.
"To achieve a 13-week topping-up interval, the Water Less battery is equipped with an electrolyte circulation system and coupled with a smart Hawker High Frequency charger, providing efficient and cost-effective recharging.
"As well as the topping-up interval coinciding with the quarterly truck servicing schedule, the user will benefit from reduced maintenance costs and lower electricity costs for battery charging."
CB Denison, meanwhile, has also improved charger performance with its high frequency battery charger for use on both lead acid and sealed batteries. Spokesman David Anderson says the charger is fully programmable, "which means a client can purchase a product for a 36 volt 500 a/hour battery and can later change it for a 48 volt 775 a/hour battery".
"We can reprogram the charger to this bigger battery without any component changes - purely a software adjustment."
Innovations like this mean businesses are able to reuse the charger, save money and lessen the impact on the environment because the battery is being reused and adjusted to the altered voltage requirements. The charger is inverter designed, which reduces electricity usage. Anderson adds this design results in lower electricity costs and reduces a business's carbon footprint.
When choosing a battery, Komatsu Forklifts seeks to improve it forklifts by reducing their total life operating costs. Harvey-Kelly says because batteries and recharging systems are part of "a complete solution", Komatsu makes sure the cost of maintenance and repair is as low as possible.
"We want batteries to have a high capacity and charging time should be as short as possible."
Philadelphia Scientific has a charging option for those with limited space or funds to purchase multiple single charging units. Its Twin Charge product modifies one charger so that it charges two batteries in sequence, reducing the need to purchase and install additional chargers.
Chris Parkinson, Philadelphia Scientific's regional director, says this product is useful when a site increases its battery power requirement when another shift is added but does not have the space or utilities for more chargers.
RejuvenationAnother area that has undergone significant advances is battery rejuvenation. It is no longer necessary to throw out batteries that appear to have run out of juice. Too often, businesses throw out batteries (and money) believing they have lost power due to sulfation.
Sulfation is an electrochemical reaction that occurs when the battery is discharged. During normal use, a battery's sulphuric acid is active between the lead plates and this creates electric current. Sulfation occurs when the electrolytes in the battery crystallise onto the plates. The loss of sulphuric acid reduces the electrolytes and transforms into water. This leads to reduced cell voltage and a reduction in charge.
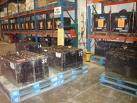 Batteries waiting to be rejuvenated |
It is accepted in the industry that 70% to 80% of all "broken" lead acid batteries have nothing mechanically wrong with them, but have sulphated plates.
Battery manufacturers usually determine the approximate number of cycles to discharge and charge the battery before it stops functioning - each battery has its own life cycle. Travis Branaman, president of US Battery Rescue Services, says if a battery stops working due to sulfation, the old remedy was to replace the cell and wait for the next one to stop performing.
"This is old technology and unnecessary," he points out. "Battery regeneration returns the sulfated battery to its original and normal condition by utilising an electro-chemical reversion process."
He explains this process can regenerate a battery that is underperforming between charges and return it to within 95% of its original specifications. "We can perform this service on the client's property."
Branaman states when the sulfation is controlled, the battery has the ability to perform for 10 to 15 years and beyond. "As long as there are lead acid batteries, sulfation will continue to be a problem."
Energy Tech, in conjunction with Forklift Battery Technology, its sister company in California, has developed a machine that it says will double the life of a battery, giving it another five to eight years on its original life span.
Paul Davy, from Energy Tech, says the BatterySAVER is new technology only just released globally and will desulfate a battery in less than 24 hours.
"There (have) been other technologies (to rejuvenate batteries) for almost a century and they have some reasonable effect," he explains. "But, it has been a long turning process and takes a month or more to desulfate a battery.
"We can do it in short order. We believe you can replicate the life of a battery by rejuvenating it. Our belief is you can effectively double the life of a battery or reduce by 20% to 25% the replacement cost."
Barloworld Handling offers customers its award-winning MACBAT regeneration system. MACBAT doubles the life of traction batteries and can bring sulphated batteries back to life. This system offers fast charging, reduced utilities costs, longer battery shift and faster, safer battery extraction.
Batterylife represents MACBAT in Australasia and Brian Hewitt, regional manager, says MACBAT has had many satisfied customers over the past three years of operation in this region.
"Battery performance and lifetime is greatly extended and cost to replace is reduced due to lower frequency of replacement. This also has a positive impact on environmental and power cost to recharge."
An option for operators to ensure a long battery life is to look for a low-maintenance battery.
Exide has entered the market with a product that reduces output on charge and reduces watering. Rob Bolton, Australian national sale manager of Exide, comments that when you take the human handling factor out, the battery lasts longer.
Instead of having to water the battery weekly, Exide's Liberator is watered every two to three months. Bolton says the biggest environmental benefit is it gases 72% less than a standard battery
.
"It is a little bit dearer, but if you look at the whole-of-life cost over acquisition price, it is actually cheaper."
As a total package, Barloworld has developed a flexible total battery management service. The service delivers 'as new' battery performance to electric forklifts for the duration of the contract. It supplies the latest low-maintenance batteries, battery charging, regeneration and extraction systems.
Another option for businesses is a system that allows monitoring of the battery's life history. Philadelphia Scientific's eGO! is a technology developed as a life history and maintenance control unit.
Parkinson says this product makes commercial sense to the whole battery market not just specialised applications. "It offers an integrated screen so the user can instantly access all the vital battery information in relation to its current condition and usage."
eGO! takes the labour out of battery watering by using an automated system that monitors the electrolyte levels and the progress of the charge cycle.
Century Yuasa told
Forkliftaction News in April (
Forkliftaction news #357) batteries are the most important component of a company's electric materials handling fleet. Incorrect battery maintenance can spell disaster for businesses in terms of reduced productivity and workflow.
The company's technical manager, Djen Kasherman, says businesses need to use quality batteries and the tools to maximise their lifespan.
Parkinson, from Philadelphia Scientific, advises there are easy ways to improve the performance of lead acid batteries that do not involve huge expenditure.
"Do not discharge the battery below the manufacturer's recommended level, monitor battery charging and usage to ensure there are sufficient spare batteries and (ensure) operators are not putting the forklift on sneaky charge during breaks.
"Allow batteries to cool down before putting them in the forklift, keep batteries clean, use deionised or distilled water to fill the battery and always, always water the battery before the electrolyte level drops to a point where the external plates are exposed."
Fitzgerald comments it is not unusual to have batteries last 10 to 15 years, if they are well taken care of and that assumes they are used for a full cycle every day.
Bowen says Linde has seen advancements in the maintenance side. "If you go back 10 years, there was quite a lot of interest in maintenance-free batteries, but the costs and technical constraints of a true maintenance-free battery has restricted its growth.
"The most interesting development we have seen is the use of low-maintenance batteries. There are different strategies being used by different manufacturers to reduce maintenance and we are talking about topping up cells with distilled water."
Environmental concerns will continue to play a growing part in the selection of batteries. Exide's Bolton says for some of their customers the environmental aspects of the products are an important consideration.
"The higher frequency chargers are a lot more energy efficient and use less power than the older type of chargers. The more environmentally aware customers see it as a benefit for their benefit." Bolton adds there are still some businesses out there that do not factor in the environmental impact at all.
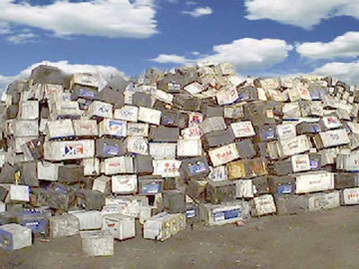 Batteries can be saved |
For Philadelphia Scientific, the environmental concerns are a good thing. Parkinson believes it forces customers to consider how long their batteries are lasting. "We can provide technology that extends the life of the battery.
"The Twin Charge helps to reduce the environmental impact of producing electricity and helps spread out the power requirements. Companies employing a battery management system have immediately noticed a reduction in their energy usage."
Lead acid batteries has its rivals in hydrogen fuel cells and hybrid power packs.
Forkliftaction News reported in July (
Forkliftaction News #371) on non-profit technology developer Concurrent Technologies Corp's (CTC) two-year demonstration program to retrofit 20 military forklifts with hydrogen fuel cells. This program's purpose is to transition the technology from lab to warehouse.
Hydrogen fuel cells will eliminate the need to recharge batteries. Forklifts will drive up to mobile filling stations and refuel with hydrogen. Some argue hydrogen fuel cells will reduce the need to dispose of batteries and will eliminate the need for multiple battery packs, battery rechargers, battery swapping equipment and personnel.
Another company hoping to take hydrogen fuel cells mainstream is Hydrogenics Corp from the US. Hydrogenics sees the materials handling market as the biggest adopter of fuel cell vehicles.
The company sees the conversion process from batteries to hydrogen as a simple one. However, at this point in the technology's development, for most end-users, the cost is prohibitive and the infrastructure to support this industry not fully developed.
Linde's Bowen says the industry is moving towards hydrogen fuel cell technology but it will take time.
"The economics of fuel cells is not there," he explains. "As an industry, (forklifts) do not have a big enough market to drive the cost down."
Bowen says Linde does not have any technical issues to bridge with fuel cells in terms of a power source. "The constraint is the cost."
However, he believes suppliers are at the whim of world commodity prices when it comes to the cost of lead.
"Essentially, the costs have gone up in the UK and the spiralling cost of lead means we have to charge," Bowen says. "Demand for lead has been high and battery manufacturers have not been able to absorb costs; this has been passed on to customers."
Exides' Bolton agrees the next big thing will be hydrogen fuel cells and most of the work is coming out of the US. "It would take only a tiny breakthrough to accelerate this technology for mainstream use. At the moment, it is just going through its testing stage to make sure it's safe."
Bolton says he cannot see lead acid batteries becoming obsolete in the near future because an alternative has not been commercially developed yet.
EnerSys's Lawton says there are two distinct schools of thought on the subject of the next big thing.
"Firstly, we are starting to see the emergence of alternative technologies for powering material handling equipment - lithium-ion batteries, fuel cells and super-capacitors are being tested by some of the leading OEMs. The benefits of these sources are good power density and very fast recharging, which means no battery changing in multi-shift applications. This could mean only one 'power pack' per truck and no investment in battery changing equipment," he says.
Lawton adds that these technologies currently have far higher acquisition costs, some need a suitable infrastructure and are still some way off from being commercially viable. "EnerSys is involved in these technologies to be sure we are aligned with the needs of our customers as alternative technologies may develop."
Davy, from Energy Tech, says lead acid batteries have been around for a long time, "a bit like petrol engines", and this will make it hard to change to a new technology like hydrogen fuel cells
.
"Lead acid batteries are cheap and a viable product that will be around for a long time."
Philadelphia Scientific's Parkinson believes the next big thing for forklift batteries will be the next big thing in automotive batteries. "In the near future the main component of automotive batteries will no longer be lead."
He explains, "This will mean a significant reduction in the cost of the main component of a forklift lead acid battery, resulting in a reduction its price.
"A low-cost lead acid battery with the technologies that have been proven to optimise it's life and performance will be difficult to move away from for all but the most specialised forklift operations."
Harvey-Kelly wants to see further reductions in maintenance in the next decade. He says it would be helpful for forklift manufacturers and end-users. "A central filling system is helpful to reduce maintenance of batteries so the cost for these systems should also be reduced," he says.
Granite Industrial Trucks hopes to see batteries that last longer in run time and longevity. Fitzgerald says they hope to see lighter weights and new technology to drive the price down substantially. "We would also like to see new designs that do away with dangerous products like lead and acid."