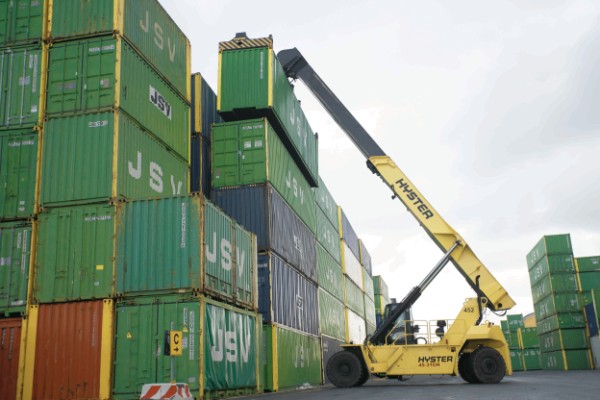 Containerisation is recovering after the global financial crisis. |
Containerised freight took a pounding during the global downturn, and is only now starting to recover. According to Containerisation International's World Container Census, container production slumped to just 350,000 units in 2009 - down from 4.25 million TEUs in 2007 and 3.25 million in 2008. This year, it's expected to climb back up to 1.5 million TEUs.
Christine Cranney looks at some of the recent developments in large forklifts, container handlers and reach stackers as global containerisation recovers.
Effect of recessionDavid Cooper, managing director of Cooper Specialised Handling, the UK's national distributor of Konecranes forklifts and reach stackers, says that without question, the global economic downturn has placed a "speed bump" on the growth of global containerisation.
"Both the shipping companies and the ports are volume-driven and once the volume has seeped away, this leads to the obvious cash flow and fixed costs issues," Cooper says.
He adds that the slump in freight demand has resulted in shipping rates falling by as much as 75% on some routes.
"Also seasonal peaks have not occurred when they should have. For example, the Christmas rush in UK ports (is usually) experienced in September as goods fill regional distribution centres, but it simply never came."
Cooper says many new materials handling equipment and services projects have been suspended or postponed. Replacements of old equipment have also slowed down. "The downturn has permitted more equipment rotation to spread, reducing hours over a wider fleet base."
Patrik Lundbäck, general sales & marketing director of Konecranes Lifttrucks, with global responsibility for the business unit, says the forklift sector of the port and shipping industry has been "severely affected" by the recession. "[The result is] a significantly lower order intake and company consolidation in the heavy segment."
Lundbäck says the company has also seen the halting or postponement of greenfield projects, a greater number of replacement orders compared to new orders, and a longer decision-making process by its customers.
Robert Taylor, vice president of operations of Mississippi, US-based The Taylor Group Inc, says just like everyone else, the private company's port equipment business was hit by the global recession in 2009.
Taylor says despite the slowdown, his company successfully launched a new machine at the end of last year.
New product developmentsDuring challenging times, companies that are able to continue investing in developing their product portfolio are likely to emerge stronger than before. Despite the gloom and doom, Hyster Europe, Konecranes Lifttrucks and Taylor Machine Works have introduced new developments to their product range.
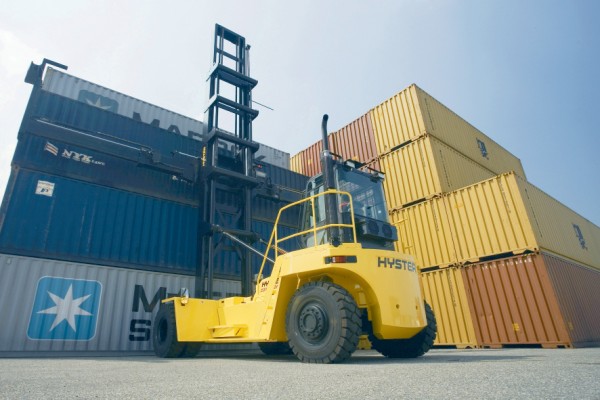 A Hyster empty container handler at work. |
Antoon Cooijmans, Hyster Europe's big trucks product manager, says a key development in Hyster's range is the new drive axle on its empty container handlers which he describes as a "major breakthrough for Hyster and the container handling industry".
"This important new development significantly reduces tyre wear and (the) cost for empty container handling operations," he says.
"No other forklift manufacturer has access to this technology in Europe at present," Cooijmans adds.
Hyster Europe currently offers AxleTech International's Xtended Tyre Life (XTL) drive axle on its H16.00-22.00XM-12EC empty container handler series. The company claims it greatly reduces costs for ports and terminals over the vehicle's life.
"Tyre changes on large container handlers are not only costly, but can be time-consuming too as the truck usually has to return to the workshop," Cooijmans explains. "Fewer tyre changes mean less downtime, plus less rubber waste means a better environmental footprint."
The XTL axle has the differential mounted in the wheel ends at each side, enabling the wheels to rotate independently, helping reduce tyre scrubbing. According to Hyster, the typical conical wear of "fixed" twin-tyre sets found on conventional axles is eliminated using the XTL axle as each wheel can rotate independently. This is not expected to interfere with full acceleration and braking power.
Konecranes' Lundbäck says his company has given its heavy forklifts (over 28 tonne capacities) a facelift.
"They now offer the driver greater visibility, especially in the rear, thanks to a counterweight with a new 'sloped' design," he says.
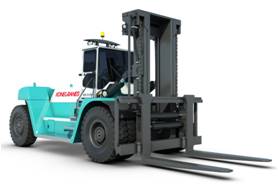 Konecranes' 32 tonne forklift now has better driver visibility. |
The cabin has also been equipped with a colour display and electronic monitoring control, which monitors all the critical components including the engine, hydraulics and gearbox. The newly introduced Eco-Drive measurement system records overall truck and individual operator truck performance as well as fuel consumption. Operator log in using a PIN, and all measurements are recorded, including total lifts, total hours, lifts per hour, fuel used, litres per hour and idling time. This provides the supervisor with a record of the driver's behaviour and habits.
Cooper says many operators believe that the engine has to rev to full rpm to achieve hydraulic performance, which is in fact a myth. "Hydraulic performance peaks at around two-thirds (of) maximum rpm, so any excessive throttle is simply wasting fuel."
The Eco-Drive system identifies operators who idle the machine unnecessarily or waste fuel. Konecranes estimates that by measuring fuel this way, users can save about GBP3,000 (USD4,496) a year in fuel costs and eliminate 770kg (1,698lbs) of carbon monoxide emissions per machine.
Also new to Konecranes' portfolio of safety features are the tyre pressure sensor and Nearguard options. Underinflated tyres are said to increase fuel consumption by as much as 10%, and the treads of properly inflated tyres can last up to 35% longer than the treads of improperly inflated tyres. The use of tyre pressure sensors not only increases safety, but also benefits the environment.
Nearguard is an RFID-based system that can identify personnel in the vicinity of the operating machinery. Instead of alerting pedestrians to the presence of machines, Nearguard warns the operator of nearby pedestrians or other equipment that have RFID identification tags. If a tag is on an individual or machine that is within 20 metres (66 feet) of the operating machine, the truck screen will automatically change to a target screen that will show the proximity and direction of the tag that has been identified. An alarm will sound and escalate as the detected object approaches the truck.
Taylor Machine Works Inc, a Taylor Group Inc materials handling company, launched the TS-9972 reach stacker last year. CEO Lex Taylor boasts that the TS-9972 is unique. "After sitting down face-to-face and discussing [the] requests of reach stacker customers, this series boasts a one-million cycle lifetime, which exceeds others in the industry. This means a maintenance savings to the customer over the life of the reach stacker."
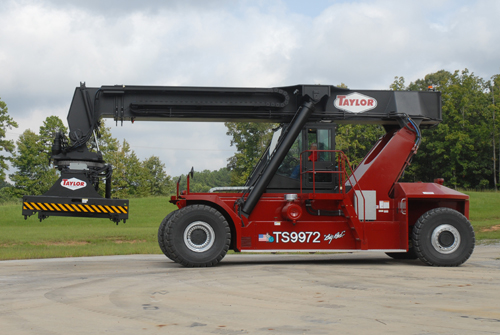 Taylor says its new TS-9972 reach stacker is unique. |
The new reach stacker can stack 9'6" (2.9 metre) containers up to 99,000lbs (44,901kgs), four-high in the first row. Options are available for stacking six-high 8'6" (2.6 metre) containers and six-high 9'6" (2.9 metre) containers. The machine features a Taylor telescopic spreader that can be hydraulically adjusted to handle containers with 20 foot and 40 foot ISO twistlock placement.
The spreader attachment includes hydraulic side shift and slew, and mechanical pile sloping adjustments. Its twin hydraulic motors and brakes enable 95° counter-clockwise and 185° clockwise rotation and allow for improved torque control and system redundancy. According to Taylor, the design features are unique and separate control of the spreader cylinders, giving greater manoeuvrability to the operator, resulting in quicker lift cycles. The spreader design also allows easy access to hydraulic cylinders, valves, hoses and electrical components, enabling quicker preventative maintenance and service diagnostics.
To avoid fatigue in heavy-duty operations, the telescopic boom is constructed from high-strength steel. A load moment indicator uses laser technology to accurately read the boom position and replaces previous technologies in Taylor reach stackers. Also, a boom angle and boom extension indicator that is a part of the electronic system provides precise control of vertical lifting via a single joystick movement.
Ergonomics of the reach truck include a "low-effort" joystick mounted on a large and adjustable armrest that provides easy control of lift/lower, boom-in/boom-out, attachment rotation and twistlock operation functions. Oversized windows and a T-shaped dashboard provide good visibility for the operator, while the all-steel, welded cabin can be hydraulically moved forward or backwards for easy access to engine, transmission, radiator and pumps, for quicker maintenance checks.
Another development for Hyster's empty container handlers this year is the new "lay-back" mast option on the H16.00-22.00XM-12EC trucks. The option enables the truck to pass under overhead obstacles like bridges or pipelines that are commonly found in port and terminal environments. Without a lay-back mast, a mast would normally be dismounted to allow the truck to pass.
Hyster has also introduced a six-high stacking option for some of its reach stacker models by fitting a longer inner boom. The RS45-31CH, RS46-36CH and RS46-41CH reach stackers can stack 8'6" (2.6 metre) containers six-high in the first container row. New standard features for all reach stacker models include a powered sliding cab for better visibility and a container weight display that enables the driver to anticipate the truck's handling capabilities before the stability and weight limits are reached.
Looking aheadKonecranes and Hyster Europe are optimistic about the future. Cooijmans says to date, machine sales and orders for 2010 are better than 2009 and he anticipates a further increase and recovery of the market. He does not, however, disclose any sales figures.
Lundbäck thinks Konecranes' greenfield projects will start moving again and there will be a higher ratio of replacement orders to new orders. "We will also continue to see consolidation and acquisitions."
Cooper says forecasts remain strong but commitments from customers are still difficult to obtain. "Confidence is required as most orders as on back of new contracts that may be awarded and which can justify expenditure."
Taylor Group Inc's Robert Taylor says the company's challenge is "to continue to convince the world that [it] is a global brand and to expand to other markets". "Taylor has an extremely bright future with the new designs we have developed and (we) plan on more new developments soon."