The forklift market is looking for greener power sources but as
Forkliftaction.com News reporter
Christine Cranney discovers, it may be a while before fuel cell forklifts replace battery-powered ones.
Martin Sinz, director of product management for Exide Technologies, the UK's largest motive battery provider, says the forklift market is increasingly focused on "green energy, energy efficiency and carbon footprint reduction" but maintains that the humble lead-acid forklift battery is still relevant.
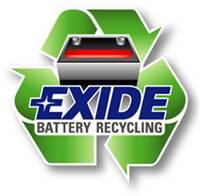 Exide is one of the largest recyclers of lead-acid batteries. |
Exide has operations in over 80 countries and claims it is one of the world's largest producers and recyclers of lead-acid batteries. It provides batteries for the transportation and industrial markets including agricultural, marine and automotive applications, telecommunications systems and railroads. Net sales for the year ended 31 March 2010 were about USD2.69 billion, with 35% of revenue from the industrial segment.
"Motive power batteries with a high current capability in charging as well as during discharge, without compromising life expectancy, are the key for economic and environmental-friendly electric forklifts," Sinz says.
He thinks that lead-acid batteries, with their weight contributing significantly to the counterbalance forklift's design - and their reliability, are the best power source for materials handling equipment. In the medium- to long-term, forklift users can look to lithium-ion batteries for "an even more economic solution". The batteries' low weight offer more freedom for forklift designers.
Bill Goodwin, Jungheinrich UK Ltd's sales director, agrees with Sinz. While he thinks that hydrogen power could become a viable option one day, he does not expect to see a significant number of forklifts in Europe powered by it for at least 10 years. "Going forward, in the short term, lithium-ion batteries will be available with the benefits of rapid charging, long running times and compact dimensions."
Lithium-ion vs Lead-acidCompared to conventional lead-acid batteries, lithium-ion power has some environmental and operational advantages. It produces zero emissions and no harmful materials are used in the battery. The technology does not use restricted pollutants like cadmium, lead, mercury or sulphuric acid. Also, it has twice the life and can store three times the energy of a lead-acid battery. They are also said to be far more energy-efficient when charging and releasing power.
Charging a lithium-ion battery is quick, enabling longer operational hours, making opearations more flexible, reducing the need for additional batteries. The size of the batteries can also be reduced significantly to allow flexible forklift design. During charging and discharging, there is less energy loss and less energy is needed to fully charge the battery.
According to Jungheinrich's research, lithium-ion batteries, with their operational and environmental benefits, are a very efficient power source for most forklift users who run a five- to six-day shift.
"We are actively working on the development of this technology and, indeed, it featured in the concept truck that formed the centrepiece of our stand at the 2008 materials handling exhibition in Hannover," Goodwin says.
Exide is also working on developing lithium-ion batteries as a stand-alone solution or as a hybrid solution, combined with other electrochemical storage solutions like lead-acid batteries.
Sinz says a hybrid battery system combining "a reliable energy source like lead-acid and a high-power source like lithium-ion" provides the best of both worlds.
However, he maintains that lead-acid batteries are still currently the most economical forklift power source and because of its good recyclability, "the best environmental energy storage solution".
Fuel cell scepticCrown and Raymond are among forklift manufacturers leading the industry in evaluating hydrogen fuel cells for their individual products
(Forkliftaction.com News #448) (Forkliftaction.com News #453). European forklift manufacturer Jungheinrich has doubts about the technology as a power source for forklifts in the near future.
Jungheinrich's Goodwin says while efforts by forklift manufacturers investigating the viability of hydrogen power have thrown up "some very encouraging results", closer analysis of the assumptions that support claims being made for the power raises question marks over its suitability to power materials handling fleets.
He explains that while hydrogen is the most abundant fuel on the planet, it has to be produced as compressed gas or cooled to a liquid form to be usable. "These processes involve the use of other sources of energy and, at the moment, the sources tend to be limited to a choice between traditional fossil fuels, nuclear power and renewable sources like wind, solar and bio-mass.
"It is widely accepted that hydrogen will only become truly attractive as a fuel once it can be produced in a way that causes zero, or minimal, greenhouse gas emissions and, of course, at a cheaper price than traditional fuels. That scenario remains some years in the future," Goodwin adds.
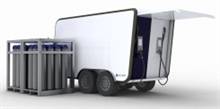 A mobile refuelling station that is used for cars and forklifts. |
As for the infrastructure to distribute hydrogen, Goodwin says there is currently only about 1,000km of hydrogen piping in the whole of Europe. As a result, hydrogen is largely transported by road, using tankers that consume energy and are polluting.
The automotive industry's enthusiasm for hydrogen has been impacted by the lack of distribution infrastructure.
"Car manufacturers are unwilling to produce vehicles without an in-place fueling infrastructure and fuel producers are unwilling to build that infrastructure without some certainty that vehicles requiring those fuels will be in operation."
As a forklift fuel, there are claims that hydrogen has benefits over traditional forklift power sources and new power sources like methanol, lithium-ion and hybrid trucks. Popular arguments in favour of hydrogen include increased productivity and lower running costs.
Goodwin argues that hydrogen's advocates claim that refueling a hydrogen-powered forklift takes about three minutes, while electric trucks are said to take 20 minutes to charge. He says Jungheinrich's electric forklifts take about 10 minutes to charge and the use of AC power extends the time between charges.
He adds that modern AC-powered machines and forklifts powered by today's lead-acid battery technology have no voltage drop problems. Hydrogen proponents like to point out that hydrogen-powered forklifts do not experience voltage drop towards the end of a shift.
He is also sceptical about cost benefits claimed for hydrogen. Jungheinrich's research indicates that to install the necesary fuel cell and charging and storage facilities to operate a fleet of 200 forklifts on hydrogen would require a capital investment at least 50% higher than if traditional fuels are used.
Goodwin points out that the technology is also not readily available although the use of hydrogen has been investigated for about 20 years.
"There have been many false dawns in the fuel cell and hydrogen sector perhaps due to the eagerness of researchers and politicians to find solutions to the very pressing challenges of energy security and climate change."
He says that "extensive and vigorous research" is needed to resolve key issues like energy and cost-efficient mass hydrogen production, site supply problems and secure storage of hydrogen.
"So the lead-acid battery currently remains the industry standard forklift power source," Goodwin concludes.
Jungheinrich engineers are working on alternative power sources that include methanol to fuel internal combustion engines. The technology to run engines on methanol is not new and has been used by the US motor racing community for some years. The forklift manufacturer is currently testing a range of tow tractors that run on the fuel. It says a prototype methanol-powered forklift is not far away.
Alternative to HydrogenMethanol, a liquid alcohol fuel mainly produced from natural gas, can use conventional storage, distribution and transport infrastructures with minimal modification, while motors running on it can achieve high thermal efficiencies and high performance levels. This makes methanol a good option for fueling internal combustion engines or, for one company, a good ingredient for a fuel cell system.
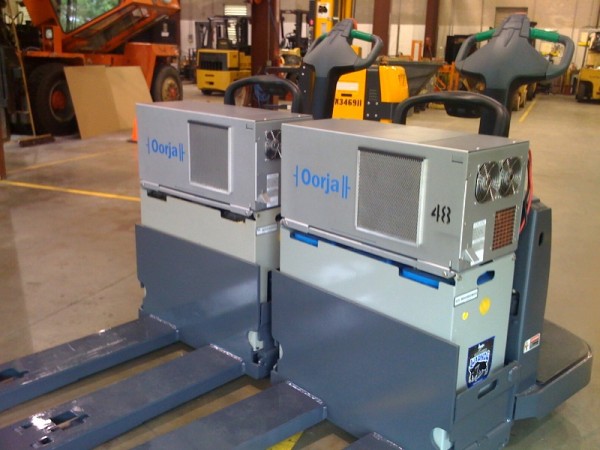 The OorjaPac is Oorja Protonics' on-board battery charger that uses a methanol-based fuel cell system. |
Sarah Johnson, Oorja Protonics' sales and business development manager, thinks that the future for battery power lies in fuel cells as on-board battery chargers "so downtime for battery change and for all charging is eliminated", resulting in improved productivity levels.
In 2007, Oorja Protonics launched the OorjaPac, an on-board battery charging system that uses a methanol-based fuel cell system. An OorjaPac continuously keeps a battery 30% to 80% charged without surge loading or the need to switch batteries. The system operates on direct liquid methanol fuel and emits clean water and minimal carbon dioxide. The Model H OorjaPac system can be refueled in less than a minute.
Oorja CEO Sanjiv Malhotra says the OorjaPac is more cost-efficient than hydrogen-based fuel cell systems as hydrogen systems require special fuelling equipment to handle pressurised hydrogen. The systems cost in the range of USD1 million. He says fuelling for alchohol-based fuel cells is safe and easy, using a simple tote dispensing system that costs less than USD10 million. The patent-protected OorjaPac can power Class 2-3 forklifts for two eight-hour shifts on five gallons (151l) of alcohol.
Last year, Super Store Industries Inc ordered over 35 OorjaPac systems for its Yale and Barrett walkie materials handling equipment in a freezer unit at the dairy product processor's California facility. The company's vice president of warehousing and transportation,Pete Blasquez, says the on-board battery charger impressed with its "productivity, safety and environmental benefits and cost savings".
Oorja currently supplies liquid fuel cells as on-board battery chargers to companies like Nissan North America, Unified Grocers, Super Store Industries, US Foodservice, Goldsen State Foods and Martin Brower. MHD Green Energy Solutions distributes Oorja's on-board charging system in North America.