Send this newsletter to an associate
 | | When will we learn that forklifts aren’t meant as lifting platforms for people. This week’s news includes another incident where someone used a forklift-supported pallet as an elevated platform – with serious consequences. In this case, the victim is the company owner, so he can’t sue his employer for inadequate training. To make matters worse, he was holding his son at the time of the accident. That’s not a great lesson for the child. It never ceases to amaze us why someone would try to use a forklift as either a raised work platform or an elevator. Don’t people know how to use ladders any more? |
|

 | |
Lower sales but incoming orders for Manitex  Bridgeview, IL, United States | Sales have dropped, but Manitex International Inc says a US government agency has ordered Liftking military container handling forklifts valued at USD2 million.
In addition, Manitex reports orders worth USD5 million for commercial boom truck cranes for the owner-operated and rental markets.
Manitex expects to ship the equipment fulfilling the new orders before the end of 2009.
Manitex reports a drop in sales to USD14 million from last year’s USD23.5 million for the first quarter ended March 31. Profit was USD61,000 in the latest quarter versus USD511,000 for the comparable 2008 period.
“Manitex Liftking container handling forklifts possess innovative features that meet strict military standards and perform in almost any terrain,” says Bob Litchev, senior vice president. “This repeat order features custom-built specifications and demonstrates the military's continued acceptance of, and commitment to, Liftking's high-quality products.”
Prior to shipment, Manitex says it tests each Liftking military machine “on a military-approved endurance track located adjacent to Liftking's military vehicle manufacturing plant. There are a limited number of test tracks in North America and having a military approved test track is an advantage.”
Manitex manufactures rough terrain forklifts, mission-oriented vehicles and specialised carriers in an 85,000 sqft (7,650 sqm) leased facility in Woodbridge, Ontario, Canada; boom cranes, sign cranes and trolley boom unloaders in an 188,000 sqft (16,920 sqm) leased plant in Georgetown, Texas; and indoor forklifts in an 86,000 sqft (7,740 sqm) leased Bridgeview, Illinois site that also houses the publicly traded company’s executive offices and operations of its crane distribution business. |  |
| Kalmar moves Ljungby employees to Lidhult  Stockholm, Sweden | Employees from Kalmar’s operations in Ljungby have started relocating to the handling equipment manufacturer’s Lidhult facility, about 40 km away, as part of the company’s restructuring plans.
The transfer, which involves about 150 people was announced earlier this year and affects Kalmar personnel working in the R&D, technology, sales, sourcing, logistics and assembling departments.
Ljungby will continue to house the service operations, finance and accounting, according to Kalmar’s parent Cargotec.
Axel Leijonhufvud, Kalmar senior vice president of product supply, says employees support and understand the need to relocate the majority of Kalmar’s operations in Ljungby.
“We have had close co-operation and negotiated with eight different unions to find the best possible solution for the employees, including early retirement plans, new positions in the company, help to find jobs outside the company, skills training and help to switch careers and set up own businesses,” he says.
Cargotec estimates that the relocation will result in annual savings of EUR2 million (USD2.9 million) and will cost about EUR4 million (USD5.7 million). Another EUR3 million (USD4.3 million) will be invested in the Lidhult facility to accommodate the new departments.
Cargotec says the transfer cost will be covered by the EUR35 million (USD50 million) it is investing in its “On the Move” restructuring operations aimed at adapting to the current market conditions, developing work efficiency. Cargotec also plans to consolidate the Hiab and Kalmar sales and service network in the European, Middle Eastern and African region.
Asked about job losses, Leijonhufvud says that since 6 November 2008, about 220 employees have left Kalmar’s Ljungby and Lidhult facilities due to “relocation and lower order intake”.
The reorganisation, a part of Cargotec’s long-term goal to raise competitiveness and sustain a leading position in the European market, will be finalised this year.
Kalmar assembles reach stackers, container handlers and forklifts in Ljungby and Lidhult. In January 2009, Cargotec employed about 380 people in Ljungby and 340 people in Lidhult. It employs 2,400 people in Sweden. |  |

| Big Lift Trucks deliver Taylor machines to Tanzania  Dar es Salaam, Tanzania | Big Lift Trucks has delivered Taylor reach stackers and empty container handlers to the Tanzania Road Haulage (TRH) container depot and packing facility in Dar es Salaam, Tanzania.
The new Taylor machines, assembled by Big Lift Trucks for TRH, include three reach stackers and six empty container handlers.
“This new equipment enhances the efficiency of our range of at least 19 Taylor machines,” says Muslim Dharamsi, owner of TRH.
Dharamsi says that the Dar es Salaam facility has used Taylor machines for container handling and packing for over 20 years.
“Taylor equipment, which efficiently handles empty and loaded containers at the TRH facility, is not only reliable and simple to operate, but these machines – unlike conventional forklifts - require simple maintenance because of the minimal amount of electronics installed in each unit,” Dharamsi explains.
The Taylor Titan RS 9968 reach stackers have centre-mounted, aluminium cabs that can be moved to access components. The cabin includes tinted and laminated front windshields, front and rear washers and wipers, as well as heaters and defrosters.
Safety features include an optional rear visibility-aid camera system, standard warning lights and an audible alarm which automatically activates in unsafe conditions.
The Taylor TEC 150 empty container handlers have a lower fan and engine speed for reduced noise and a high capacity cooling system. There are also electronic diagnostics on the engine with a fault code history for quick troubleshooting and a built-in shutdown system for the engine and transmission as standard.
Delivered over a two-year period, the order cost about ZAR23 million (USD2.5 million). TRH has been dealing with US-based Taylor for over 25 and has about 28 Taylor machines. Big Lift Trucks assembled the new machines and helps to maintain them.
Big Lift Trucks is the exclusive distributor for Taylor machines, Meclift forklifts, Mobicon container handlers and Capacity terminal haulers in Southern Africa. It has recently introduced the Meclift ML 1612R variable reach truck series to the market. The reach truck has a double fork system that can handle four pallets at the same time and fully load a 20 foot container with only two lifts. |  |
| Suits cite patent infringement, personal injury  Madison, WI and Philadelphia, PA, United States | Raymond Corp has sued two Jungheinrich entities for patent infringement, while a manager operating a Mitsubishi forklift has taken action against the equipment lessor and manufacturer for personal injury and product liability.
Greene, New York-based Raymond says that the design for the mast construction on the Jungheinrich ETR 320 reach truck infringes US patents that were issued to Raymond in August 2006 and July 2008.
Raymond’s patented design for the mast minimises obstruction to a forklift operator’s field of view, according to the suit.
Raymond attorneys filed the litigation on 20 May in the US District Court in Madison, demanding a trial by jury and seeking monetary awards from the two defendants, equipment distributor Jungheinrich Lift Truck Corp of Richmond, Virginia and designer-manufacturer Jungheinrich AG of Hamburg, Germany.
Raymond competes directly with Jungheinrich products in the electric forklift truck market.
Attorneys with the Milwaukee, Wisconsin law firm of Quarles & Brady LLP are representing Raymond in the case, which was assigned to Magistrate Judge Stephen L Crocker.
In the other litigation, an attorney says Thomas Catlett was using a Mitsubishi FB18NT to move pallets of muffins to a box truck in a Philadelphia warehouse of his employer, specialty food distributor BT Enterprises Inc, on 7 May 2007.
According to the lawsuit, Catlett “stopped the forklift behind the truck, engaged the emergency brake, dismounted from the forklift and walked to the back of the box truck at which point the forklift rolled into the plaintiff and violently struck him in his back and leg pinning him between the pallet of muffins on the forklift and the truck”.
The suit says: “The warning system on the forklift failed to operate when the plaintiff dismounted from the forklift”, and Catlett injured his lower back, right knee, calf and leg, and neck and experienced “severe nervous shock”.
Catlett sued owner-lessor Accurate Lift Truck Inc of Bethlehem, Pennsylvania and manufacturer Mitsubishi Caterpillar Forklift America Inc (MCFA) of Houston, Texas. An attorney with the Plymouth Meeting, Pennsylvania law firm of Morris Clemm & Heleniak PC filed the suit on 22 April in the US District Court in Philadelphia, asking for a jury trial on the claims of personal injury and product liability. The case was assigned to Judge Stewart Dalzell.
The suit cites more than a dozen examples of the “negligence and carelessness” of Accurate Lift Truck in maintenance, service, safety and standards-compliance matters relating to the forklift. Accurate leased the forklift to BK Enterprises, which employed Catlett as a manager.
MCFA designed and manufactured the electric three-wheel cushion-tyre counterbalanced forklift, which has a lifting capacity of 3,500 pounds (1,575 kg). On 26 May, MCFA asked to be removed from the case.
In 1992, Mitsubishi Group’s industrial manufacturing and trading units and a Caterpillar Inc industrial subsidiary pooled their technological and financial resources and established MCFA. The joint venture’s plant manufactures Mitsubishi and Caterpillar forklifts in Houston. |  |

| Shaw says recession good for business Halifax, United Kingdom | Shaw Handling says the economic downturn has been good for its business and it is still on track to launch its “revolutionary” forklift range this year.
The Abu Dhabi-based manufacturer established by British-born David O’Callaghan initially planned to launch its iLift range in the second or third quarter this year (Forkliftaction.com News#405). It is now planning to introduce the forklifts to the market in the fourth quarter of 2009.
O’Callaghan tells Forkliftaction.com News that Shaw’s inaugural launch consists of forklifts over 10 tonne capacities, empty and laden container handlers and reach stackers.
“The launch will see the first new designed iLift with capacities of 10-18 tonnes and five- and six- high empty container handling trucks that will be based on our new design,” he explains.
In the next four years, Shaw will launch 20,000-28,000kg forklifts and seven- to eight-high empty container handlers. The iLift family of trucks will be fully constructed based on a modular design.
O’Callaghan says that forklifts built on a traditional platform and used in normal operation are usually rebuilt after 20,000 to 40,000 hours of usage. “This means they are completely stripped to the chassis and all major parts replaced and then it is painted. The amount of time it takes to do this can be halved with the new modular construction trucks,” he says.
Shaw explains that companies are now looking to reduce costs and are open to new developments to help them do so.
“Customers want more flexibility and less downtime. The new Shaw iLift meets these demands and customers who have had the concept explained find the new way appealing. They can now cut the number of trucks needed in their fleets.”
Shaw has also attracted people with vast experience to join the company because “the current job uncertainty means employees are more willing to join a new company” and are looking for new opportunities in the market.
O’Callaghan adds that Shaw has been contacted by companies from the US, Australia, Germany, Italy, Brazil and India expressing interest to partner as dealers in joint-venture partnerships as the forklift market is now more competitive.
“This has been promising and the companies who sign up first will be where the launches will take place. Italy is the first with a number of trucks possibly sold there,” O’Callaghan says.
Shaw is currently talking to Tailift about a joint venture, which will see the Taiwanese forklift manufacturer producing the iLift range for sale in China and Taiwan.
“These talks might take some time but we are hopeful that an agreement will be finalised by the end of the year,” O’Callaghan says. |  |
| Toyota to launch world-first IC hybrid forklift  Tokyo, Japan | Toyota Industries Corporation (TICO) will launch what it claims is the world’s first internal combustion (IC) hybrid forklift in the Japanese market in December 2009.
The “Geneo Hybrid” was developed in response to growing awareness of global warming and high fuel prices.
TICO says the IC hybrid forklift is targeted at the mid-size (over 3 ton load capacity) electric forklift market in Japan.
“While sales volume of electric forklifts has gained a majority share in the Japanese market, mid-size electric forklifts only represent 6% of all mid-size forklift sales,” TICO says in a statement.
This is because of the upfront investment required for high-capacity and high-voltage batteries and the installation of charging facilities. Users may also find the battery changeover required in multi-shift operations challenging.
Using Toyota Motor Corporation’s hybrid technology, TICO developed a hybrid system to match forklifts that travel while handling a load and frequently start and stop.
The hybrid system combines a diesel engine, electric motor and battery power. According to values measured by TICO based on Japanese industrial standards, the Geneo Hybrid reduces carbon dioxide emissions and fuel consumption by 50% and performs like a 3.5 ton diesel-powered IC forklift. |  |

| Forklifts stolen from building materials distributor Springfield, MA, United States | Police in Springfield are investigating the theft of four forklift trucks from the Springfield distribution facility of building materials wholesaler North Pacific Group Inc.
Police indicate the forklifts have a total value of about USD120,000.
The theft occurred during the Memorial Day weekend and was reported to police on 26 May. Police responded on 25 May to an activated burglar alarm at the business, but the absence of employees on the holiday prevented an early determination of the loss.
Employee-owned North Pacific is based in Portland, Oregon, operates more than 50 sales and inventory locations across the US for distribution of building materials, industrial and hardwood lumber, structural and engineered panels and other specialty products, and generates sales of more than USD1 billion. |  |
| Sidewinders show their stuff in Star Trek  Hollywood, CA, United States | Two Sidewinder ATX-3000 omnidirectional forklifts make cameo appearances in the science fiction Star Trek movie, and the technology is slated to appear in another film.
Sidewinder manufacturer Airtrax Inc, however, cannot benefit. An investor group halted operations, controls uncompleted units and liquidated the plant and other assets. The stock AITX.PK has a 52-week range of USD0.001-0.02.
In the Paramount Pictures Corp film, forklifts manoeuvre slowly, loading cargo in the shuttle bay for transport to the spaceship USS Enterprise.
The Sidewinders and other vehicles “were chosen for their unusualness combined with their clearly well-designed utilitarianism”, says Star Trek production designer Scott Chambliss. Sidewinder filming occurred in a Goodyear blimp hanger in Irvine, California during the spring of 2008.
“The movie has generated a huge amount of buzz,” says Nicholas Fenelli. “We know that Sidewinder has a cult following.”
While chief of Airtrax operations, Fenelli made trade-out agreements in early 2007 with television program producer Beyond International Ltd of Artarmon, New South Wales, Australia. Producers at the Discovery Channel in Canada, the ProtoType This! series and the Mythbusters series were in the loop, Fenelli says. “Someone at Paramount studios saw a production and was impressed. He proposed the Sidewinder to Star Trek's director, who was also impressed.”
For product placement, Fenelli sent two demonstrators through dealership H&E Equipment Services of North Las Vegas, Nevada.
“Things went so well that another arrangement was made to use the Sidewinder in the Paramount production GI Joe: the Rise of the Cobra,” scheduled for 7 August release, Fenelli says.
After filming, the Sidewinders went to Lift Works Inc of West Chicago, Illinois, which offers 12 Sidewinders for rent.
Sidewinders “give people more manoeuvrability” and the technology has a future, says Marty Starck, owner and president of Lift Works.
Fenelli is president of Vehicle Technologies Inc of Trenton, New Jersey, which was formed in January 2008, employs four, retains two consultants and specialises in the design and manufacture of electric vehicles utilising omnidirectional-drive and alternating-current motor technologies.
Swedish engineer Bengt Ilon at Mecanum AB designed and patented an omnidirectional wheel technology in 1973, but “the level of control in the early 1970s was way too expensive to make the system work,” Fenelli notes.
The US Navy purchased Ilon’s technology through an investment intermediary in the 1980s and advanced it at the naval surface warfare centre in Panama City, Florida. The idea: achieve mobility in tight shipboard quarters. In January 1996, the Navy transferred the technology to a predecessor of Airtrax and other firms for USD2,500 each under co-operative research and development agreements.
Four 21-inch (0.52m) sets of polyurethane-covered 45-degree peripheral steel rollers make contact with the floor and are attached to corresponding wheels.
The platform with tines can move in lateral, diagonal and rotational directions. Instructions from an operator’s joystick feed a microprocessor that coordinates four independent electric motors, each of which controls one wheel.
Airtrax founder and chief executive officer Peter L Amico Sr carried the technology torch but died in August 2006. Temporarily, Fenelli served as acting CEO.
As a development-stage company, Airtrax encountered challenges including operating losses, funding requirements, production development, commercial market acceptance, protection of patent rights and establishment of distribution channels.
Airtrax produced Sidewinders in a Blackwood, New Jersey plant from September 2005 through March 2006 and was anticipating volume output from FiLCO GmbH’s Mulheim, Germany factory, previously a manufacturing site of Clark Material Handling of Europe GmbH. Airtrax agreed in 2004 to acquire FiLCO, but, in 2006, FiLCO filed for insolvency in January and Airtrax terminated the agreement in February.
In June 2007, CEO Robert Watson signed restatements of Airtrax 2005 and 2006 financial reports that were filed with the US Securities and Exchange Commission (Forkliftaction.com News #315).
“My efforts have resulted in a lot of exposure for the Sidewinder and the omnidirectional technology, but just a little too late for Airtrax,” Fenelli notes. “Sadly, the company had halted production of the Sidewinder lift truck (after making about 70 units). All operations finally ceased in March 2008, the employees separated and the facilities closed.” Five remaining Sidewinder dealers are located in the US, southern Europe and Israel. Excalibur Design Services Inc of Trenton supports Sidewinders in the field.
At Vehicle Technologies, “we are not in a position to market and develop equipment,” Fenelli says. “We will build one-off for someone paying for the development.”
Work on the movie ─ the 11th under the Star Trek franchise ─ began in 2005, and filming occurred under secure conditions in late 2007 and early 2008. Spyglass Entertainment and director JJ Abrams’ Bad Robot Productions created the 127-minute USD150-million film under the auspices of Hollywood, California-based Paramount. Gross revenues exceed USD209 million from Star Trek’s 7 May theatrical release through 31 May.
That exposure shares the concept of omnidirectional forklifts with a wider audience. |  |

| Briefs  | Manitou appoints new chief
Ancenis, France
Manitou BF’s supervisory board has appointed Jean-Christophe Giroux as chief executive officer, replacing Marcel Claude Braud.
Braud will become the non-executive chairman of the board. The reorganisation will be submitted to Manitou shareholders in an EGM held in the northern hemisphere autumn.
According to Manitou, the decision reflects the wish of the group’s founding family to focus on the governance of the company and its strategy, and return to a legal structure based on a board of directors.
Manitou says the contraction of its order book on an international level, the acquisition of GEHL in the US and the global financial crisis, all contributed to the appointment.
Yale honours top performers
Greenville, NC, United States
Yale Materials Handling Corp has recognised its top performing dealers at its 15th annual dealer of excellence awards ceremony at the company’s American marketing headquarters.
Seventeen dealers from all over the US received awards for their achievements in customer satisfaction, dealer performance, general management, truck sales, short-term rentals, aftermarket sales, and parts and service operations.
Solideal and Loadstar seek donations
Sri Lanka
Industrial tyre manufacturers Solideal and Loadstar are seeking RS10 million (USD212,854) in donations to enable the Solideal Loadstar Rehabilitation Trust (SLRT) to finance relief assistance for the displaced people of Sri Lanka.
About 200,000 people who have fled the formerly rebel-controlled areas in northern Sri Lanka are housed in a camp in Vauniya awaiting re-settlement.
SLRT, which was formed to assist victims of the 2004 tsunami, has been re-activated to provide relief to the displaced people.
To donate, go to http://www.belconsulrehabfund.org/donations.php |  |
Sample of used equipment for sale: | Search 5276 listings in the Marketplace | |
Heli |
H35D03-352 |
2008 |
United States |
USD 69999 |
Details |
Linde |
H35D04 |
2002 |
Netherlands |
EUR 13500 |
Details |
Linde |
T18 |
2000 |
Germany |
EUR 850 |
Details |
JLG |
G9-43A |
2002 |
United States |
USD 32900 |
Details |
Toyota |
6FGCU15 |
1999 |
United States |
USD 2900 |
Details |
Baumann |
EVS40-31.5 |
1994 |
Germany |
EUR 5990 |
Details |
Hyster |
E50XM2 |
2003 |
New Zealand |
NZD 15250 |
Details |
Crown |
20MT130A53051 |
- |
Australia |
AUD 7000 |
Details |
Caterpillar |
DP40K |
2005 |
United States |
USD 25000 |
Details |
Yale |
GP060TG |
2002 |
Germany |
EUR 5750 |
Details |
Hanselifter |
RS35 |
2007 |
Germany |
EUR 18500 |
Details |
Toyota |
7FGCU32 |
2005 |
United States |
USD 7200 |
Details |
Nisan |
APH02A25U |
- |
Australia |
AUD 6800 |
Details |
Hyster |
S50XM |
2002 |
United States |
USD 5900 |
Details |
and thousands more... Click here to include your used forklifts, stackers, telehandlers, container handlers, attachments etc. |  |
| Two fall as forklift-supported pallet kicks out Cascade, IA, United States | Jerald Pasker, 32, and his son, Gary, 6, fell about 25 feet (7.5 m) after the father with the boy in his arms tried to step onto a forklift-supported pallet that kicked out, according to the Jones County sheriff’s office.
The pair’s 29 May fall occurred down a shaft onto a concrete floor at a Cascade area high-security communications facility that Pasker owns.
Pasker uses the forklift to lower equipment into an underground area.
The Paskers, who reside in Monticello, Iowa, were transported to the University of Iowa Hospitals and Clinics in Iowa City. The father absorbed the brunt of the fall, and the son escaped without serious injury. |  |
| Restored forklift a labour of love for repairer  Bay Roberts, Canada | A former General Motors dealership technician with a penchant for restoring vintage items has almost single-handedly restored a 1985 Toyota forklift.
Paul Short ,who started automotive repair business Specialty Repairs in Bay Roberts, Newfoundland, Canada with his wife Kathy 14 years ago, tells Forkliftaction.com News the couple “didn’t think they’d end up doing some of the things they are doing today”.
Besides repairing cars, Short and his wife were asked by their customers to do machining and welding work. Before long, they had accumulated all types of specialty tools.
“Our regular day consists of vehicle repairs, welding and machining but after a little while, I decided to start restoring some unique items I would find around the local area,” Short says.
The items included old vintage gasoline pumps, Coca-Cola vending machines and coolers, vintage Honda motorcycles and children’s pedal cars.
“We built a special 1,000 sqft (93 sqm) building just to display all the stuff and all our customers enjoy viewing it all when they drop by for a visit,” Short says.
The couple soon discovered that they needed help moving disabled vehicles and other heavy items that were brought in for welding.
“Living in Newfoundland and being on an island, we don’t get a lot of choices when it comes to buying used machinery but eventually I found a Toyota forklift.
“It was a rough-terrain machine and that’s just what I needed.
“[However] it had spent the last 20-plus years working at a local fish plant and was very rusty. It looked terrible and needed a lot of work,” Short explains.
Short says he just wanted to make the 1985 model “look better” but when he bought it for CAD2,000 (USD1,885), his regular customers who saw it would say “I bet you’re going to do something really cool to that machine”.
“Well, for me, that meant I had better not disappoint them and restore it as good as I can,” Short adds.
The project took on a personal meaning for Short when Kathy located the forklift’s serial number on its frame and discovered that the forklift was one month and two days older than his youngest son Daniel.
Kathy’s role in the project was “the most important one”, Short says. Before restoration work could begin, Kathy did “all the searching for parts, manuals and even researched the forklift itself”.
“We had trouble finding the serial number on the lift and after many hours of research she located the area on the lift in which to find it. Without the serial number, we would have come to a dead end before we even started,” Short says.
Short started restoring the Toyota by removing all the parts to be rebuilt or replaced. He used high-pressure water to remove the old coat of paint and a self-built, big sand-blaster to cut through the rust. He ordered new mast bearings and new cylinder kits. Some of the hydraulic cylinders were sent for re-chroming.
As the original Toyota engine hood was too expensive to replace, Short fabricated a new engine hood and rebuilt the motor by replacing all the gaskets, oil pan, bearings, rings and valve stem seals. With the transmission, he replaced the filter and fluid. He rebuilt all the brake lines and replaced all the hand brake cables and the ratchet.
Short then installed new tyres, and primed and painted the forklift. Due to the machine’s weight, all the work was carried outside his shop. Before winter arrived, he used his new Kubota tractor to push the not-yet-running forklift into his shop.
While it was indoors, Short fabricated a sun visor, a rear light bar and a custom storage box for the forklift out of checkered plated aluminium. “I even placed checkered plate around the frame and it was really starting to take on a new look.” Short says.
He then replaced the steering wheel with a custom wheel and redid all the wiring on the forklift. After that, he added special lights with guards that he had fabricated and air horns, and installed new dash gauges with LED lighting.
To complete the forklift, Short removed its worn-out charging system with its outdated external voltage regulator, and installed a new GM alternator with a built-in voltage regulator. He also custom built new mounting brackets.
“After that was done, I had the motor up and running and it was sounding sweet, especially since I removed the old exhaust system and custom mounted two chrome exhaust stacks in the rear of the lift,” Short says.
Short says he accomplished all this with an investment of CAD4,500 (USD4,150) in parts and materials and during his spare time over four months. The forklift is now used on a daily basis.
Short adds that he learnt from his experience that “if you’re going to restore a forklift, it would be much better to have another forklift help with the lifting”.
“By the time I purchased our new Kubota, the heavy parts of the restoration was completed,” he says.
But the hard work has paid off. “I am very pleased with the outcome. I have a machine that complements our business and is practical to own. The old forklift actually looks like a new one. Customers love seeing it and some even took photos of it,” Short says.
To view photos of the restoration work, go to: http://www.flickr.com/photos/15602393@N05/ |  |
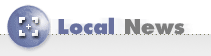 | |
| No light on Hyster rumours  Melbourne, Victoria, Australia | Adapt-A-Lift has refused to comment on reports it has been appointed the new distributor of Hyster in Australia.
While many in the industry are anticipating an announcement soon, the Melbourne-based company says it has "no comment" on the speculation.
Adapt-A-Lift has registered a number of companies called Adapt-A-Lift Hyster in Western Australia, Victoria, New South Wales, South Australia and Queensland, but it will not concede that the registrations are proof that a deal has been sealed, saying that it has registered other business names as well.
Founded in 1979, AAL is a privately owned forklift company comprising a national forklift fleet of over 5,600 units with company-owned offices in Victoria, Queensland, New South Wales, South Australia and Western Australia.
Hyster is a subsidiary of NMHG, one of the world's largest forklift manufacturers with brands including Yale and Sumitomo. In addition to a worldwide distribution network of independent Hyster and Yale retail dealerships, NMHG operates wholly owned dealerships in certain markets including Hyster South East in Victoria, Hyster North in Queensland, Hyster South in South Australia and Hyster West in Western Australia. |  |
| Used forklift market down but not out  Australia | Australia’s used forklift market is taking a beating with prices sagging as a result of excess stock.
Some blame the government’s capital investment scheme, introduced in December 2008 (Forkliftaction.com News #399), which they say is luring traditional buyers of second-hand forklifts to purchase new equipment and benefit from the tax rebate.
“We have lost deals directly as a result of this scheme,” says Cliff Chadwick, owner of Chadwick Forklifts which has been operating for the past five-and-a-half years.
He says used forklift dealers are getting hit four-ways: “Not only does the government subsidy work against us, but we’re battling the global economic crisis, and on top of that, we’ve got big companies selling off their excess rental units which is flooding the market. And finally, there are a number of companies going broke which means their stock is ending up on the auction and depressing prices even more.”
Chadwick says the price of trade-ins has diminished and it’s tougher all round doing business.
But on a hopeful note, he says his company is surviving. “In the last month, things appear more buoyant – I think there’s light at the end of the tunnel.”
But while it’s clear that prices for used equipment have softened, not everyone believes the government incentive is the real culprit.
Damien Garvey, national sales manager for NTP Forklifts Australia, which deals in both new and used equipment, tells Forkliftaction.com News that the used equipment market has been suffering over the past couple of years, and well before the government incentive was introduced.
“The main reason for this has been the factory-owned representatives in our industry are buying up marketshare, flooding the market with cheap new products and devaluing the used equipment market,” he says.
NTP still accepts trade-ins but values have dropped, says Garvey, adding that the values of returned rental fleets have also decreased due to the flooding of new equipment.
He says that the continuous unreserved auctioning of these fleets shows that most companies are suffering the same effects.
And it’s not just Australia’s used forklift market that is depressed. Steve Mackay of Central Forklift Group in New Zealand tells Forkliftaction.com News that the New Zealand market is being impacted by the leading brand-holders dumping used equipment on the market at reduced prices as they struggle with the impact of the recession.
His company is still accepting trade-ins but at a reduced price compared to last year. The company is also carrying more stock as businesses are returning non-contracted equipment as a result of the recession.
Paul Bebendorf, part owner of RP Material Handling in Coffs Harbour, NSW, which sells both new and used forklifts, doesn’t believe the government incentive scheme is having any real effect on the new or used markets.
“While traditional buyers of used equipment may decide to opt for a new Chinese forklift, it has more to do with price than the incentive.”
He says the company still accepts trade-ins and does not believe that prices for used equipment have depressed significantly – “it really depends on the type of forklift being traded”.
He says the company has been selling more of both new and used forklifts lately, perhaps a sign that the economy has started to recover.
Red Australia’s Leonie Perry tells Forkliftaction.com News that the company has not experienced a decline in Komatsu second-hand equipment sales due to the incentive scheme. “Any downward movement, we believe, is due to the market in general rather than being a direct result of the government’s tax break.”
In favour of the incentive is Jenny Ritchie of Flexilift, exclusive distributor of Hyundai forklifts in Australia. She tells Forkliftaction.com News that the company’s focus is on selling new forklifts and, as a result of the government incentive, business is pretty steady.
“It’s good for the industry,” she says, “but not for the used sector as it’s just not viable to buy a second-hand unit when you can get a tax rebate on a new one.”
She adds that the company still accepts trade-ins, most of which are sent off to auction. “Prices for trade-ins are much on par with the previous year,” she says.
Not according to Peter Ewing, sales manager for material handling supplier Hastings Deering. “Prices have definitely dropped for used equipment. We are offering 25% to 35% less on trade-ins because otherwise we just can’t sell it.”
He says the company, which sells both new and used Caterpillar forklifts, has benefitted from the government’s incentive scheme – “it’s certainly helped and we have got sales directly as a result of it. Sales are still down on last year but we haven’t lost marketshare.” |  |
| Larger container ships on NZ port agenda  Auckland, New Zealand | Ports of Auckland has gained resource consent for berth deepening and associated wharf works at its Fergusson container terminal.
Managing director Jens Madsen says the works will cement the port’s ability to cater for the next generation of container ships, carrying 5,000 to 7,000 TEU.
Ports of Auckland has already dredged its shipping channel in preparation for the larger ships, and three of its existing container cranes, the largest in the country, are capable of servicing the vessels.
The port is equipped with eight container cranes, three more than any other port in New Zealand.
“The three newest cranes have a 50 metre outreach which, taking into account the additional fendering required for larger vessels, gives us the ability to service ships 18 containers wide,” says Madsen.
The berth deepening and wharf works will take between 24 and 30 months to complete. |  |
| Take control of cash flow issues  Melbourne, Victoria, Australia | Australian firms are taking steps to improve their cash position and ensure their sustainability against the challenging economic backdrop.
Figures released recently by Dun & Bradstreet reveal that the number of business-to-business debts referred for collection has increased by almost 20% year-on-year, and their dollar value is up by almost 50%.
According to Christine Christian, D&B's CEO, Australian firms have recognised that a relaxed attitude towards collections is no longer sufficient and that effective cash-flow management is a critical factor in ensuring the ongoing sustainability of business.
"A number of Australian firms are now acting on their arrears relatively quickly when previously they would have allowed them to accumulate for lengthy periods of time. These executives are seeking to address both current outstanding payments and longer term arrears, which is increasing the level of debt being referred for collection.
"With close to 80% of business failures said to be the result of poor cash-flow management, this is a smart move which could be the difference between a business continuing to operate profitably or falling into irreversible financial distress."
More than 10% of firms in each state are now classified as a higher risk of paying their trade accounts in a delinquent manner.
These findings indicate that the economic downturn is likely to be prolonged and difficult for many firms, with cash flow likely to tighten further in the months ahead. |  |
| Rail freight study in Adelaide  Adelaide, South Australia, Australia | The Australian government has awarded a AUD3 million project to professional services company, GHD, to examine rail freight movements to and through Adelaide and surrounding areas.
The study aims to help develop a basis for long-term strategies to improve the efficiency of the national freight network and address the local community’s concerns about noise, congestion and safety.
A project reference group including ARTC (Australian Rail Track Corporation), Freight Rail Operators Group and relevant local councils has been established to ensure consultation with key stakeholders and the community. A discussion paper setting out the various options is expected to be released by the end of July 2009, with the full study report completed by the end of October 2009. |  |
| Reducing port delays is vital to trade  Melbourne, Victoria, Australia | The time taken to get products from factory to ship is absolutely vital, with every day that a product is delayed before being shipped reducing a country’s trade by more than 1%.
That’s according to research undertaken by the World Bank and Deakin University which looked at how time delays as a form of trade costs affect international trade in 98 countries, including Australia.
According to Dr Cong Pham, an expert on international trade at the university, merely reducing the time it takes to get goods from the factory gate and onto a ship would have as much a positive impact on a country’s trade performance as reductions in tariffs.
“One day of delay is equivalent to a country distancing itself from its trade partners by 70km on average. The impact is twice as much for landlocked economies,” says Pham.
Surveys showed the whole process of documents preparation, customs clearance and technical control, ports and terminal handling and inland transportation takes, on average, 10.7 days in the OECD countries and 23.3 in East Asia and the Pacific.
While Australia’s required time for export, which is nine days, is less than its neighbours like New Zealand (10 days) and Indonesia (21 days), it needs to do much better in order to catch up with the best OECD performers in this respect. Export procedures only take five days in Denmark and Singapore and six days in Luxembourg, Hong Kong, Netherlands and the United States.
“The main reason for Australia’s underperformance is that an exporter in Australia has to fill out, on average, six documents while those in the OECD, on average, fill out 4.5.
“Comparatively, the cost of exporting in Australia is more expensive, with the average cost being USD1200 compared with USD902 in East Asia and the Pacific and other OECD countries where the cost is USD1069. To improve our performance, we would have to reduce any delays at our ports further and reduce the paperwork.”
Pham adds that while Australia can’t reduce the spatial distance that separates it from the world, it can promote its trade substantially by simplifying its export procedures. |  |
Send this newsletter to an associate
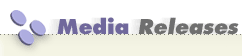 |
| The TEP Technica and RAEDER-VOGEL® partnership goes from strength to strength  | As a world leader in the production of warehouse truck wheels and tyres RAEDER-VOGEL® is renowned for the quality and durability of their products and for a service level that is second to none. These attributes were never more important than they are in today’s global downturn as truck users increasingly seek to increase utilisation, minimise downtimes and reduce lifetime costs. The message is clear. Better products last longer. Better products are not merely those that comply strictly with a high specification - though this is absolutely critical. It is also about making the right choice for a specific application. The RAEDER-VOGEL® range of wheels includes options to suit all possible applications - from cold stores to slippery floors, from high speed to high load, from explosion risk environments to the supermarket shop floor. No one offers a more comprehensive range than RAEDER-VOGEL®.
Click here for the full text of this release, including pictures. |  |

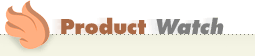 |

|
|

Tip off Forkliftaction.comDo you know something our readers should know? Write to news@forkliftaction.com or provide information anonymously here.



Upcoming Events | 1. The Smart Supply Chain Technology ShowSydney, Australia 10-11 June 2009 2. Big Rig Expo - 2009Tulsa, Okhlahoma, United States 22-24 October 2009 22/10/2009, 23/10/2009, 24/10/2009 3. U.S. Open Forklift Rodeo & Safety ExpoSpringfield, Ohio, United States Fri - Sat 30-31 October 2009 4. 2009 Queensland Safety ShowBrisbane, Australia 16 - 18 June 2009 5. Material Handling & Logistics (MHL) 2009Auckland, New Zealand 22-23 July 2009 6. Chesapeake Forklift Safety RodeoWest Friendship, MD, United States 18th July 2009 7. Hot Legal Issues in this Economy ....Free Seminar.Bridgewater, New Jersey, United States 16th June 2009 8. Handling ExpoCairo, Egypt 22 – 25 October 2009 |





Editorial Calendar 2009
|
January
Rough Terrain forklifts
February
Safety products in MH
March
Forklift Market in Canada
April
Tow trucks
May
Forklift Market in the United Kingdom
June
Fleet & Asset management
July
Narrow Aisle forklifts
August
Industrial tyres/wheels
September
Forklift batteries and power solutions
October
Side loaders
November
Explosion-proof forklifts
December
Forklift Market in India
|
















|